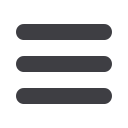

COVER STORY
May 2015
MODERN MINING
23
extensive design and planning collaboration
between the teams to ensure that redesign dur-
ing manufacture and assembly was limited to
the bare minimum, thus avoiding time delays.
Barloworld Power committed to delivering
the first motivator to site a full two months
ahead of schedule so that it could be used to
move the first assembled rope shovel off the
assembly pad on the mine. This meant that the
unit had to be on site before the road embargo
on abnormal goods in Namibia, which was
effected on 3 December 2013. As the unit took
four days to get to site, the delivery schedule
was extremely tight.
Barloworld Power’s Customised Solution
Centre, together with the installation team,
pulled out all the stops to ensure that this hap-
pened and the unit was delivered to the Walvis
Bay branch of Barloworld Namibia on Friday
29 November 2013. The second motivator was
handed over on schedule by 31 January 2014.
Optimum design
The initial design of the unit incorporated all
the equipment and the engine in a single enclo-
sure, but during the detailed design phase this
proved to be impractical for several reasons:
the trailer became too cumbersome and
costly to manufacture;
the risk of fire damaging the electrical equip-
ment if it all shared a common enclosure
was deemed to be too great;
the risk of dust contamination on the electri-
cal equipment was too great;
the size of the generator meant that if this
solution was pursued, an 18 m long trailer
would be needed. This would have made
transport and movement of the unit on the
mine prohibitively difficult as well as being
very costly to build and maintain in the
long term;
the overall height of the unit on a standard
trailer would have resulted in an unaccept-
ably high centre of gravity, increasing the risk
of a rollover on a banked gradient.
With these issues in mind, it was decided
to design a step deck with a lower centre of
gravity and the generator mounted to it. The
electrical equipment enclosure with the fuel
tank is mounted separately on the gooseneck.
This proved to be the most successful arrange-
ment as it brought the centre of gravity down
by nearly 2 m and reduced the overall length
by 4 m, resulting in a unit that is stable and
relatively easy to manoeuvre.
The trailer has to be towed by a suitably
sized horse with a special low range gear-
box to successfully cope with the low speeds
needed to walk the rope shovel and negotiate
the gradients of an opencast mine. Owing to
the identical design of the trailers, two identi-
cal horses were needed.
A comprehensive fire detection and sup-
pression system was installed in the engine
compartment and a full detection system in the
electrical compartment.
The compact medium voltage switchgear
is also state-of-the-art, with IP 67 encapsu-
lated ingress protection of the environmentally
friendly vacuum switching contacts and the
MV conductors. This characteristic enables the
switchgear to be submerged in water for three
days without any negative effects on the main
conductors.
The durability of this section of the switchgear
was one of the main reasons for its selection as it
is highly suitable for a dusty desert environment.
The very low voltage control circuitry eliminates
potential hazards associated with dust or mois-
ture contamination. These design measures do
not mean the equipment is maintenance free and
a strict maintenance schedule is in place.
A motivator moves a
Cat 7495 electric rope
shovel.
Barloworld Power
committed to
delivering the first
motivator to site
a full two months
ahead of schedule
so that it could be
used to move the
first assembled
rope shovel off
the assembly pad
on the mine.