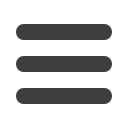

RESEARCH AND DEVELOPMENT PROGRAMS, PATENTS AND LICENSES
11
11.1 Research and Development
processmercury waste, asbestos waste, organic waste not accepted at the Centraco
incineration facility, acidic waste, activated metals, powder waste and others.
Designed to meet the needs of AREVA’s waste retrieval, cleanup and dismantling
projects, some of these developments are also of great interest to our Asian partners
and customers, particularly for the packaging of radioactive sludge and waste
and for contact maintenance and cutting scenarios and technologies used in the
cleanup of buildings and reactors.
An important area for improvement is the inclusion of digital and connected tools in
all operations in this field. Illustrations include the deployment of a product lifecycle
management tool (PLM) to manage the configuration of facilities undergoing
dismantling at the la Hague site, the use of touch tablets to monitor projects or to
collect and use operating experience, and the development of tools to simulate
equipment operations. In particular, a simulator for polar crane operations was
developed in 2016 to train operators on this highly specialized equipment. The first
presentations and training given in 2016met with success with the entire profession.
The development of other modules is planned, and the prospects of using such a
tool opens up opportunities for the sale of new services in this segment.
R&D activities of AREVA Projects in the fuel cycle
AREVA Projects is a key partner for the research and development programs of
the business units. Specifically, AREVA Projects brings the engineering skills and
expertise needed in the phases which precede the industrial implementation of
products and processes resulting from R&D in the entities: feasibility studies and
front-end engineering and design of innovative facilities; final development and
qualification of simulation tools and of processes; products and equipment for
use in the fuel cycle facilities of AREVA or its customers; and operator support.
The Beaumont-Hague development and testing laboratory (HRB), an AREVA
Projects technical center located near the la Hague recycling plant, houses the
activities of the two main divisions: Technology, which develops specific tools and
response scenarios and also develops and qualifies mechanical equipment; and
Chemistry, which deals with a broad range of topics, including the development
and qualification of chemical engineering equipment and of waste treatment and
packaging processes (cementation, vitrification, drying, etc.) for AREVA’s different
entities.
R&D ACTIVITIES OF AREVA NP
R&D activities of AREVA NP in nuclear fuel
Improving nuclear fuel performance
AREVA NP conducts ambitious research and development programs to adapt its
products to its customers’ performance requirements, up to high burnup levels, with
the goal of continually improving fuel reliability during operations and guaranteeing
the highest level of safety. These research and development programs involve:
p
developing new fuel designs, in particular to optimize thermo-hydraulic
performance and enhance operating robustness;
p
adapting to changes in nuclear fleet operating conditions, whether for the
cladding or structural materials (new alloys for greater resistance to corrosion
and deformation) or for the fuel itself (advanced microstructures to reduce the
release of fission gases at high burnups);
p
responding to questions from the safety authorities concerning fuel behavior in
accident situations, in particular during an earthquake, requiring the development
of new methods in an environment of changing safety standards and of new
accident-tolerant fuel concepts (ATF);
p
developing advanced codes and related methods for PWR and BWR fuel
incorporating the neutronics, thermos-hydraulics and thermos-mechanics of
the fuel rod;
p
working with scientific partners, notably the CEA, to improve the modeling of
physical phenomena occurring in the fuel during irradiation, and integrating
these models into advanced simulation software.
AREVA continues to develop a new generation of more robust fuel assemblies
with enhanced performance and safety margins for boiling water reactors (BWR)
and pressurized water reactors (PWR), called Atrium™11 and Gaia respectively:
p
following the first Atrium
TM
11 test assemblies, now in their fourth irradiation
cycle in the core of the Gundremmingen reactor in Germany (RWE), irradiation
continues on other assemblies loaded into the Leibstadt reactor in Switzerland
(AXPO) in 2013 and the Olkiluoto 1 reactor in Finland (TVO) in 2014;
p
the first Gaia test assemblies delivered to the Vattenfall electric utility in Sweden
completed their fourth irradiation cycle in the Ringhals 3 reactor core;
p
work to make Gaia test assemblies available in 2018 for EDF’s 14ft (N4) reactor
made significant progress in 2016with the completion of mechanical and thermo-
hydraulic tests on full-scale assembly mockups;
p
deployment of the Gaia and Atrium™11 technologies in the United States
continues with the start of test assembly irradiation, initially by two U.S. utilities
in 2015;
p
development work continued on various types of ATF cladding, including
chromium-coated zirconium alloy cladding, as well as on a disruptive concept
of SiC-SiCf composite cladding, notably with the introduction of the first test
components in Switzerland’s Göesgen reactor in 2016. This development was
the subject of a number of partnerships, in particular with the CEA, EDF and
the U.S. DOE.
R&D activities of AREVA NP in reactors and services
Widening the range of light water reactors and supporting
their deployment
EPR REACTOR
Work carried out in partnership with EDF to optimize the EPR reactor design’s
economic performance was completed in 2014. This paves for the way for definition
of an optimized design basis which the proposal and project teams may use to
define adaptations needed to meet customer specifications.
The start of the Hinkley Point C Project in the United Kingdom represents a
culmination of this cooperation. AREVA NP’s R&D team mobilized to define and
qualify the improvements made to this project, such as pumps with hydrodynamic
seals that simplify the architecture of sealing systems in the event of a loss of
electrical power, and a more compact instrumentation and control system.
126
2016 AREVA
REFERENCE DOCUMENT