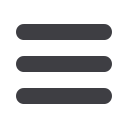

M
AY
2016
71
AR T I C L E
SMS Group
xx
Machinery and plants for the production
of oilfield tubulars
By Dr Ing Hansjörg Hoppe and Dr Ing Hans Pelster, SMS Group
The use of oilfield tubulars made from high-alloy materials is
always necessary when one of the following concentrations is
exceeded in the oil or gas stream:
•
pCO
2
concentration > 1,500psi
•
Cl- concentration > 250mg/l
•
pH
2
S concentration > 10psi
•
Temperature > 390°F
Commonly used high-alloy and corrosion-resistant materials
are duplex steels (22Cr-5Ni), super-duplex steels (25Cr-7Ni-N),
super-austenitic steels such as alloy 28 (28Cr-32Ni), nickel-
based alloys such as alloy 825 (42Cr-21Cr-3Mo) or titanium
alloys such as Ti Grade 5 (Ti-6Al-4V). The material to be
chosen for a particular application depends on the corrosion
conditions.
Currently most manufacturers are limited in the production
of large-diameter, high-alloy oilfield tubulars that have to be
cold worked in order to achieve the strengths necessary for
such deep wells. There is a growing demand for tubings and
casings up to outside diameters of 10
3
/
4
" (273.1mm) and
appropriate lengths from 30 to 40ft (9 to 12m).
The SMS group as a system supplier offers its customers
tailor-made solutions. Hot-finished, high-alloy oilfield tubulars
or mother tubes that still have to be cold-formed can be
produced in the diameter range 33.4 to 323.9mm (nominal 1
to 12") on extrusion press lines from the SMS group. Cold-
rolled tubes in the diameter range from 5 to 280mm can be
The rising worldwide demand for oil and gas is leading to
ever deeper well depths. Well depths of 25,000ft (7,620m)
and more are no longer unusual. Generally speaking,
increasing depths mean increasing temperatures and
pressures. Many high-pressure and high-temperature
(HPHT) wells with temperatures up to 400°F (204°C) and
pressures up to 20,000psi (138MPa) have already been
drilled. At the bottom of the well, the conditions become
even tougher.
The real challenges for the materials from which the
oilfield tubulars are produced arise during the oil and gas
extraction. Depending on the temperature, pressure, flow
velocity and corrosive constituents in the gas stream,
such as H
2
S and CO
2
, the use of low-alloy steel, high-
alloy stainless steel, nickel-based alloys or titanium
alloys is necessary.
produced on SMS group cold pilger mills. The SMS group also
offers complete hot and cold processing lines as a package
solution. These include, in addition to the core machines such
as extrusion press lines or cold pilger mills, machines for billet
preparation, pickling and degreasing facilities, finishing and
testing equipment – in some cases from subcontractors.
Production of high-alloy oilfield tubulars
Stainless steels or nickel-based alloys are melted in an electric
arc furnace melting process or in induction furnaces under the
exclusion of air, and are further processed in downline plants
by argon-oxygen decarburisation (AOD) or vacuum-oxygen
decarburisation (VOD).
If the batch size allows, continuous cast starting material
is used; otherwise chilled cast material is used. Simple
austenitic steels can be extruded directly without prior hot
forming. Higher alloy materials must first be forged or hot-
rolled in order to break down the linear casting structure and
achieve a homogeneous microstructure.
The product portfolio of the SMS group includes all the plants
for primary and secondary metallurgy for the melting of high-
purity stainless steels and nickel-based alloys as well as the
necessary casting plants. After casting, the round ingots are
rolled to the required billet size or forged on radial forging
machines from the SMS group.
In the final work step, the rolled or forged bars have to be
peeled in order to create the surface quality necessary for the
extrusion process. Peeling is performed on special machines
from the SMS group.
1 Rotary gas furnace
2 Induction furnaces
3 Glass lubrication
4 Piercing press
5 Hydraulic station
6 Final heating
7 Glass lubrication
8 Extrusion press
9 Water quenching
10 Cooling table
Figure 1: Layout of extrusion press line