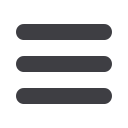

I
nspectIon
& T
esTing
www.read-tpt.comM
ay
2012
111
Thermal field seam evaluation
TUBES that seem to be completely
physically correct can fracture in use. The
reason for this, especially in ERW welding
processes, is too low or too high heat input
or material faults. Commonly used eddy
current or ultrasonic systems are limited in
detection of such errors.
The evaluation of seam quality by using
its thermal field opens up new possibilities.
Even penetration faults or seam asymmetry
can be recognised in the running production,
and every inch of the tube is controlled and
documented. The ThermoProfileScanner
(TPS) from HKS-Prozesstechnik makes this
possible.
Operation next to the welding spot is
possible through a glassless, gas purged and
water cooled construction. From the recorded
thermal data the welded seam’s basic
parameters are calculated. The threshold is
freely adjustably and therefore adaptable to
the respective process. The basic parameters
like seam position, width, symmetry and
temperature are the base to recognise such
weld defects as lack of fusion, cold welds,
pores or seam offset.
The TPS measures the infrared intensity of
radiation of the cross-section of the welded
seam during solidification with a frequency of
100 to 400Hz. This allows welding speeds of
up to 180m/min. As a result, irregularities can
be recognised of dimension less than 1mm
in the thermal signature. The sensitivity of
the TPS allows it to measure a temperature
range from approximately 650 to 1,350°C.
For weld inspection purposes, the
characteristic of the heat-affected zone (HAZ)
depends directly on the weld seam quality.
Therefore unacceptable seam irregularities
and weld defects will be detected, marked and
sorted out.
HKS-Prozesstechnik GmbH
– Germany
Fax: +49 345 68309 49
Email:
info@hks-prozesstechnik.deProfessional Chinese
manufacturer of slitting lines,
tube mills, tube toolings, etc.,
since 1980’s, the one-stop
solution for the global market
with efficient after-service.
HDCT
Slitting Line
www.slittinglinelms.com info@lmsmachinery.comNon-destructive testing
CONTRÔLE Mesure Systèmes designs,
develops and manufactures for more than
25 years a complete NDT range of products
in eddy current and ultrasonic testing
methods which comprise high performance
instruments and systems, probes and
transducers, and accessories.
All the systems meet quality standards
such as API, ASTM, and DIN and be used
on-line and off-line.
CMS’s product line includes: eddy
current range: eddy current instruments
mono or multi channels branded Zet@;
special software, acquisition systems high-
speed data with real-time visualisation and
accessories; rotating heads RotoETscan,
rotating
systems,
magnetising
and
demagnetising units; eddy current probes
and coils for specific applications and
standards designed to meet customer
specifications.
Ultrasonic range: ultrasonic instrument
UTscan-100 combines high performance
with great versatility; immersion tank for
pipes inspection; ultrasonic rotating heads
RotoUTscan for tube inspection for in-line
high speed flaw detection and dimensional
measurements of ID/OD/thickness; with
its know-how and its experience, Contrôle
Mesure Systèmes can provide also from
design to manufacturing, complete turn-
key machines with associated mechanics;
through its products and its remote assis-
tance, Contrôle Mesure Systèmes provides
all over the world, quality and productivity
solutions for industrial applications.
Contrôle Mesure Systèmes
– France
Email:
contactcms@cmseddyscan.comWebsite:
www.cmseddyscan.comEddy current probe
INNOSPECTION Ltd has introduced a novel
approach to the inspection of swaged carbon
steel boiler tubes with the development of a
specialised rotational Eddy Current probe.
The swaged carbon steel boiler tubes are
inspected for internal longitudinal cracking.
This form of crack occurs on the internal
surfaces of the pull-bent sections of the
tubes, propagating directly from the adjacent
external tube joining seam (vein) welds.
The Innospection probe is collapsible in
order to overcome the restricted tube bore
entry formed by a tube-sheet swaged joint.
The probe eddy current sensors remain
collapsed going through the swage. Once
inside, the eddy current sensors are rotated
by an electrical motor and are forced
outwards by the centrifugal force.
Innospection Ltd
– UK
Email:
info@innospection.comWebsite:
www.innospection.com