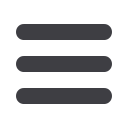

wiredInUSA - March 2016
29
An Airbus team has been recognized
for developing an efficient new method
to repair fiber optic cables.
Lighter than traditional metallic wiring
and offering much higher bandwidths,
fiber optic cables are applied
throughout the company’s modern
commercial jetliners – integrated in
taxi aid cameras, cockpit systems and
many other key components. However,
when non-conformities are discovered
in a cable during installation, the repair
is a costly and time-consuming process.
Project co-leader Laetitia Mennebeuf,
a fiber optics specialist from Airbus’s
systems
engineering
department,
explained: “Before, if damage was
found, the entire cable and surrounding
harnesses needed to be removed so
that the repair could be performed in
a shop outside of the aircraft. This took
ten hours to do, and in removing the
harness, other cables and wiring could
get damaged.”
She added: “One of the more common
non-conformities concerns the contacts
at the twoends of acable. If thecontacts
were deficient, they had to be cleaned
and polished or remanufactured at the
shop floor laboratory.”
“Working with our supplier, AVOptic,
we developed new, portable tools
that re-polish the contacts,” explained
fellow project co-leader Nadège
Brunaud-Martinerie, an engineer from
Airbus’ manufacturing engineering
department.
“Because they’re portable – and
battery-powered – the new tools can
be brought on board the aircraft
and repairs made without disturbing
the other installers. We use the same
processes and get the same results and
quality as before, but…repair time is cut
from ten hours to two hours.”
The 18-month project received a 2015
award for excellence from Airbus.
Onboard fiber
repairs
INDEX