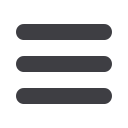

Mechanical Technology — October 2015
23
⎪
Computer-aided engineering
⎪
The combination OptiStruct
and Inspire puts simulation and
optimisation within reach of
mainstream designers.
to reductions in cost, development time,
material consumption, and product weight,
says Smith. “The program’s optimisation
capabilities are sought after in multiple
industries including aerospace, automo-
tive, heavy equipment, architecture, and
consumer products,” he adds.
Altair is focused on the development
and broad application of simulation
technology to synthesise and optimise
designs, processes, and decisions
for improved business performance.
Privately held with more than 2 300
employees, Altair is headquartered
in Troy, Michigan, USA, and operates
more than 40 offices throughout 22
countries. Today, Altair serves more
than 5 000 corporate clients across
broad industry segments.
The solidThinking set of tools is
aimed at structural analysis and op-
timisation, as a precursor to full-scale
CAD (pre-CAD). “Inspire’s power is in
early design exploration and puts high
level analysis tools in the hands of
designers so that CAD users can focus
on the detailing without worrying quite
so much about the structural or functional
engineering side,” Smith exclaims. “Any
company looking at lightweighting in prod-
uct design has three basic options: using
advanced materials; changing the topology/
geometry; or redesigning the entire product,”
he adds. “solidThinking Inspire focuses on
the topology/geometry optimisation option
and, with Inspire 2015, users can do this
faster and more easily and accurately than
ever before,” he concludes.
Earlier this year, solidThinking an-
nounced the signing of channel partnership
agreements with productONE, Rapid3D and
Access CAD/CAM to introduce the South
African market to solidThinking Inspire.
q
With solidThinking Inspire 2015, Smith says users can do topology/geometry optimisation faster and
more easily and accurately than ever before.
tibody dynamics technology, combined
with advanced optimisation algorithms,
OptiStruct lets engineers analyse and
optimise structures and mechanisms for
their strength, durability and noise and vi-
bration harshness (NVH) characteristics.
While OptiStruct has the muscle to tackle
the most complex design problems in
great detail, Altair’s solidThinking Inspire
unleashes the power of simulation and
optimisation for concept designers during
early idea validation.
Inspire masks the complexity sur-
rounding simulation and optimisation
and makes it accessible to a less simu-
lation-savvy audience. For example, the
software treats tasks like creating mesh-
es and boundary conditions in a way
that’s friendly to non-experts so they can
immediately dive in. Through its intuitive
user interface, Inspire performs such
tasks with the click of a button, opening
up a world of optimisation possibilities
for design engineers without any hand-
holding or direction from time strapped
simulation experts. In addition to its
intuitive user interface, Inspire delivers
simulation and optimisation capabilities
that meet the needs of design engineers.
It can depict stress distribution, displace-
ment, or deformation characteristics like
traditional CAE tools, plus Inspire helps
design engineers determine the optimal
load path and where materials can be
removed to improve the design.
In a continuous engineering workflow,
design engineers work with Inspire to
come up with concepts that meet basic
performance requirements, while CAE
experts pick up where they leave off,
leveraging OptiStruct’s more advanced
functionality to further refine designs.
Polaris, a snowmobile manufacturer,
is driving efficiencies and design improve-
ments throughout its engineering work-
flow thanks to the use of OptiStruct and
Inspire. On a specific chassis project with
pretty rigorous weight reduction goals,
Inspire was tapped during the concept
stage to quickly identify the basic shape
and engineering, while OptiStruct was
brought in to refine the shape for manu-
facturability and stress requirements.
Inspire and OptiStruct were also paired to
help evaluate the weight reduction poten-
tial of using aluminium as a substitute for
steel in several subassembly structures.
Not only did OptiStruct and Inspire
help Polaris engineers substantially re-
duce the weight of the structures, it also
greatly reduced the number of design
iterations – from 10 to 12 cycles down
to 5 or 6.
Simulation and optimisation work
best as an integrated team that is put
to use continually throughout the design
workflow. By democratising the practices
so they are within reach of mainstream
designers, not just simulation experts,
companies can achieve dramatic engi-
neering efficiency that will steer them on
a course to greater innovation.
q