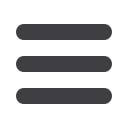

⎪
Pump systems, pipes, valves and seals
⎪
Mechanical Technology — September 2016
15
Figure 2: Pumps in parallel often have their discharge valves throttled to ensure that the current drawn is
kept below the maximum motor rating. The author has found numerous instance where the current drawn
is far less than maximum motor rating and fully open valves do not overload the pump motors.
We sequentially opened each of the
valves and checked that the amps drawn
were less than the maximum motor rat-
ings. Unthrottled, all the motors were
well within their ratings. In addition,
when all the valves were 100% open,
we were able to achieve the required
flow rate with one pump shut down
completely.
Running five pumps instead of six led
to savings of 258 kW, which translates
into 2.1 GWh in reduced energy costs
per year – and this return from a zero
cost intervention.
Why were the pumps being throttled?
There may have been a reason as some
point, but things change and if the con-
sequences are not being measuring, how
can pump operators know that throttling
every pump still has any beneficial ef-
fect? Even if there was a valid reason
for throttling at some point, shouldn’t
it have been investigated to determine
whether that reason still applied? Or do
we continue to throw away two-inches of
prime fish because this is what we have
always done?
But what happens in cases where the
motor is drawing more amps than its al-
lowable maximum. Surely this is a case
when throttling a pump can be justified?
Wrong! There are other ways to fix
such situations and none of them involve
wasting energy through throttling. This is
a topic for the next article, however, when
we will discuss energy efficient ways to
reduce pump output, such as trimming
the impeller, reducing the pump speed
or changing the pump.
q