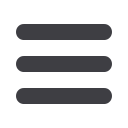

59
The survey of Keebler was conducted in 1999 and sponsored by the Council of
Logistics Management. 355 US-companies participated. They could select from a list
of 70 metrics, which metrics they used. It was found that there was a strong focus on
external and internal metrics as well as on cost. On the other hand, it showed a low
coverage of metrics to control operative logistics. A delimiting factor for low coverage
was a missing IT support or missing information in IT systems [27].
The survey of Liebetruth was executed in 2004 on the basis of 19 expert interviews
with responsible supply chain managers of selected companies in Germany. The aim was
to find out which elements formed the information basis for performance measurement
in supply chains. It was found that even though the focus was on supply chain
performance measurement, “classical” logistics performance elements such as inventory,
delivery reliability, actual vs. budgeted (logistics) cost and accuracy of planning systems
were the most used performance elements in the surveyed companies [34].
The survey by Weber et al. was conducted in the period between July and
September 2011 and sponsored by the German Logistics Association. 180 answers from
logistics service providers and 251 answer from industrial and trading companies were
recovered, representing a return rate of 37% and 44% respectively. It was found that
progressive companies achieved better results in forming a consistent system of KPIs
integrating the operative and strategic level as well relating its own performance to
that of their most important external partners. Also successful companies focus on few
important KPIs report them timely to the responsible managers and adapt the KPIs
when new challenges in the companies’ context arise [56].
Some strengths add to the widespread use of KPIs:
• The use of KPIs is easy to communicate. The famous saying “What gets
measured gets done” is commonly associated with KPIs.
• A system or a set of KPIs offers a multidimensional view on certain aspects. And
it is possible to flexibly adapt the system by adding new KPIs or eliminating old
ones.
But some weaknesses can also be diagnosed when analysing the usage of KPI systems:
• There is a great risk of creating a data graveyard because, when adapting a KPI
system, often only new KPIs are added. An argument against eliminating is
that there is no more possibility to compare new developments with the past.
Also, the risk of inconsistencies increases.
• Moreover, with an overflow of KPIs, the interpretation of every KPI not
obvious throughout the whole company or supply chain. So it is questionable
whether the KPIs will generate impact.
• There are associated risks of particular KPIs that are not defined along the
above stated guidelines. As there are examples within each guideline this is not
discussed here.
• As there is no standardised structure and often no explained connection
between the KPIs, it is not possible to check whether important developments
or explanations are missed because no KPI for this event was generated. Also
due to a lack of standardisation, it is difficult to compare the KPIs of different
companies.