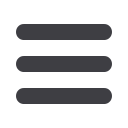

travelling too close to the crest edge
(
Figure 14
). Here, a solid safety berm has
been erected for vehicles. In addition, a
line of cones has been erected to warn of
the crest edge and its Red No-Go Zone. A
worker transgressing this zone can easily
be seen and corrective action taken.
Conclusion
The crest edge risk in surface mines and
quarries varies from virtually no risk for
low inclined benches found in many clay
mines, to high risk for high benches that
are vertical with poor crest conditions.
Each operation has to perform a full
site-specific risk assessment determin-
ing both the probability of a crest failure
and fall of worker/machine and its conse-
quence. The assessment should include
the impact (literally) onto the toe of the
bench below.
It is suggested that where the risk
level is found to be moderate to high,
a physical barricade should be erected
to warn workers and pedestrians of the
high risk area close to the crest. On oper-
ating benches, safety berms composed of
rocks or chippings are not normally nec-
essary. All benches that are not in opera-
tion should be closed with a physical
barricade that prevents vehicular access;
for example, a solid rock berm.
Along haul roads and especially
inclined haul roads (ramps), the risk of a
machine driving over the crest is signifi-
cant and this risk can be reduced by the
erection of a safety berm, typically the
radius of the largest wheel.
It is important that this berm does
not add to the rolling rock risk and there-
fore should be typically composed of
homogeneous, non-binding material, eg
13 mm crushed aggregate. The edge of
the berm should be at least 1,0 m from
the crest edge. Regular gaps should be
left in the safety berm to prevent water
ponding and allow for safe viewing into
the quarry and examination of any ten-
sion cracks.
The barricade should be marked by
a Competent Person on every operating
bench to warn of the high risk crest area
and form a Red No-Go Zone between the
crest and tension cracks.
MQ
About the author
Consultant rock engineer Dave Fenn. holds a Master
of Business Administration (MBA) from the UCT
Graduate School of Business; a Graduate Diploma in
(Rock) Engineering, University of the Witwatersrand;
AA Advanced Certificate in Rock Mechanics; Chamber
of Mines Certificates in Rock Engineering (including
Surface Mining); Dip CSM (HND) Mining Engineering,
Camborne School of Mining (UK). He is a SANIRE and
SAIMM member.
He has 25 years mining experience of which 24
have been in rock engineering in soft coal measures
as AngloCoal’s section head from surface to 280 m
deep, to hard rock gold and platinummining (tabular
and bulk UG methods) from surface to 2 600 m deep
as a rock engineering officer.
He opened a successful independent rock
engineering consultant practice (Applied Rock
Engineering cc) in 2006, and has gained extensive
open-pit experience augmenting his underground
work. This includes the compilation of over 50 slope
COPs, lecturing for a SAQA-accredited training com-
pany, performing operation geotechnical audits and
a geotechnical service, including geotechnical feasi-
bility studies and pit slope design for many leading
mining organisations.
TECHNICAL FEATURE
SAFETY BERMS