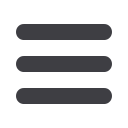

S
eptember
2011
125
›
W
elding
e
quipment
A simple to operate, low cost
orbital welder
THE use of orbital tube welding equipment is
mandated in a few select, global industries,
such as semiconductor, bio-pharmaceutical
(North America, Western Europe and Japan),
nuclear, and aerospace. These industries,
when applying the use of orbital welding,
specify in their standards (for example,
ASME/BPE 2002 & SEMI F78) not only a
high degree of repeatable weld quality but,
in addition, a high degree of documentation
and verifiability of the orbital welding process.
In the construction of a new
pharmaceutical plant, tube welding quality
control inspection records are an important
part of the overall documentation required
for validation of the completed facility before
operating approval is granted by regulatory
agencies. Every operator is required to
make a test weld (coupon) at the beginning
and end of each shift to ensure that the
equipment is functioning properly. This has
driven the development of QC software that
monitors all weld parameters in real time.
Boundary limits can be placed around each
parameter: for example, rotation speed
might be monitored for any deviations from
programmed values by more than 1%. Weld
data can be logged and printed out by an
integral printer, or stored and downloaded to
a USB flash drive for transfer to QC records.
These features, which are critical
to certain industries, come with a price,
however. The features require hardware and
software which drive up the cost. There
is also the price in complexity. Numerous
set-up screens are required to define the
QC reporting and data storage/printout. The
many options cannot be depicted with simple
symbols and require text. Text requires
multiple language selection, and so on.
There are other industries that utilise a
large volume of process piping (stainless
steel in particular). The food processing,
dairy, and beverage industries generally fall
in this category. They do require a uniform
and completely penetrated weld at all times,
no matter how these results are achieved (be
it manual or mechanised weld processes).
One development that has resulted in
increased use of orbital welding are clean-
in-place (CIP) systems. To allow cleaning
of equipment without disassembly the weld
surfaces must be smooth enough to avoid
entrapment of product or cleaning residue.
These industries require sanitary/hygienic
tubing systems, but do not necessarily have
to weld to a “code”. Although they do follow
general guidelines and good manufacturing
practices (The 3A Sanitary Standards; AWS
D18.1 “Specification for Welding of Austenitic
Stainless Steel Tube and Pipe Systems in
Sanitary (Hygienic) Applications) for welding
sanitary tube systems, worldwide few
government agencies have adopted these
as mandatory standards. Certain companies
have adopted them, but there is no industry
requirement.
In the majority of cases, when asked
what precludes the use of orbital tube
welding as the primary joining process of
their process lines, the perceived high cost
of the equipment ends being the primary
response. Surveys have shown that the
price of an orbital welding system is 2-3
times higher than a fabricator or contractor,
servicing these industries, is willing to
pay. The complexity of controls for the
welding systems on the market dictate on
site training, adding further cost that may
represent 10% of the system price.
To offset this concern over equipment
cost and simplify the orbital tube welding
process, Magnatech has introduced an
innovative solution to orbital tube welding
with its modular, EZ Orbital Welding System.
The Model 517 is a tube welding controller
that integrates the operation of standard,
commercial GTAW power source with the
weld head. The customer can use his existing
power source, allowing him to weld both
manually and automatically. The controller
has an intuitive symbol-based, touch screen
user interface. Operation is as simple as
selecting tube size and wall thickness, and
pressing the Start switch on the head. The
operator can adjust set parameters by a
percentage override to accommodate tube
lot variations. A USB port allows for software
upgrades and updates.
The Model 517 operates a new line of
tube welding heads with digital control of
rotation speed regulation, ensuring perfect
repeatability. The heads use replaceable
360° contact tungsten holders, a moulded
silicone switch panel, and incorporate flip-
top viewing ports for convenience.
The head is equipped for water-cooling
and can be connected to a standard water
circulator. However, it can be operated
without one. If the head temperature
exceeds a limit, the operator is notified
that he has to reduce his duty cycle, or
attach a water circulator. A training DVD
provides all the instruction necessary for
the simple-to-operate system.
Magnatech
– USA
Website:
www.magnatechllc.comProfessional Chinese
manufacturer of slitting lines,
tube mills, tube toolings, etc.,
since 1980’s, the one-stop
solution for the global market
with efficient after-service.
HDCT
Slitting Line
www.slittinglinelms.com info@lmsmachinery.comAUSB port allow for software
upgrades and updates
The modular EZ Orbital
Welding System