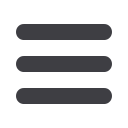

S
eptember
2011
83
›
T
echnology
U
pdate
solder contours, negatively affect costs and
quality of the final product. The answer to all
of these production problems is consistent
further development, eg of “solder batch
contours”, which can be implemented using
the forming technology of Rosenberger AG.
Both axial forming technology on the new
forming machine generation flexFORM RU8-
12-18 and radial profile rolling technology on
the rolling machine series RW20 guarantee
a high level of quality and performance in
rough industrial everyday operation or in
development centres.
Technical feasibility is now provided by
servo-electrical drives, since they are able
to move along complex ramps, in contrast to
the “blunt” moving forwards and backwards
of hydraulically driven tools. The flexForm
RU8-12-18 is not just a further development
and merger of Rosenberger’s predecessor
models RU8-12 and RU18, but rather a
completely new machine concept that
combines the advantages of its respective
predecessors while also containing many
years of experience and insights of the
company’s customers. The PLC-based
CNC control enables free programming of
all dimensions, paths and motions up to
0.01mm, forming force and speed. Servo
controllers ensure soft and precise running
through the programmable speed profiles for
best material flow control. Any and all material
properties can be included in programming of
the flexForm RU8-12-18 and considered in
the production process. Thus, not only simple
flanges, beads, reductions or expansions can
be produced, but complex pipe end shapes
can be generated as well.
Tool and programme changes can be
implemented in less than 5 minutes and are
measured fully automatically. The servo-
electrical asynchronous drives with an axial
working force of up to 180kN are low-
noise and -maintenance, energy saving
and do not generate great exhaust heat,
which leads to additional benefits in the
ergonomics and energy results.
A globally unique novelty is the compact
build and machine concept with its vertical
tool alignment (no more than 16, also multiply
rotating tools) and no use of hydraulics at
all; this makes the machine being easy to
transport and saves a lot of footprint space.
The offer includes the machine as a single,
hand-operated version, master-machine and
fully automatic forming device. The robot
connection can be used to best integrate the
machine into a fully automated system and
to use it flexibly. The fully automated joining,
eg of flanges, Ü-nuts, Ü-bolts, O-rings, and
holders is a standard application. The model
version DT (DoubleTool) enables concurrent
processing of two parts, which doubles the
daily output or cuts the cycle time in half.
Depending on task and parts geometry,
the clamping jaws can be installed to act
vertically or horizontally.
The clamping unit, type of tool change
and force of the axial, servo-electrical
asynchronous drive can be selected and
set up in modules. Possible attachment jaws
enable protection of pre-formed contours
or multiple contours. Several rotating tools
can also be set up, so that various rotating
processes like profile rolls, planes, chamfers,
thread shapes, etc can be processed with
great efficiency in a single programme run.
Rosenberger AG also provides the
required process-safe forming tools.
Interfaces that are already integrated, eg for
BDE-recording, network connection for data
back up and profibus interface for connection
to existing systems correspond to the latest
state-of-the-art. Remote maintenance can
reduce standing times and downtimes to a
minimum and thus warrant the basis for quick
reactions by Rosenberger’s service team.
Rosenberger
– Germany
Website:
www.rosenbergerag.comPutting the smarter heat to smarter use
www.efd-induction.comThis is not a pipe.
It’s actually an entry ticket to huge markets. Be-
cause what you’re looking at is a longitudinally weld-
ed pipe that’s been normalized to oil and gas pipe
standards. But there’s a catch. Normalizing isn’t
easy. Especially for today’s gauges and alloys. It de-
mands expertise in metallurgy, control software and
precise heat delivery.
The good news however is that these are areas in
which we specialize—making us a leader in pipe
weld-seam normalizing. Also, with more than 50
years’ induction heating experience, we’re experts at
using technology to open new commercial opportu-
nities for our customers.
EFD Induction is Europe’s no 1—and the world’s
no. 2—induction company. Our systems are used to
weld, normalize, anneal, harden, temper, braze,
melt, forge, bond, cure and pre- and post-heat.
So whatever your pipe normalizing needs, you
can turn to us for a solution. And since we’re present
around the world, that solution is probably closer
than you think. Contact us today. There’s a vast oil
and gas pipe market out there. We’ll help you get a
share of it.
Learn more about our pipe welding and normaliz-
ing solutions at Fabtech 2011—visit us at Booth 348.
Putting the smarter heat to smarter use
www.efd-induction.comThis is not a pipe.
It’s actually an entry ticket to huge markets. Be-
cause w at you’re looking at is a longitudinally weld-
ed pipe that’s been normal zed o oil and g s pipe
standards. But there’s catch. Normalizing isn’t
easy. Especially for today’s gauges and alloys. It de-
m nds expertise in metallurgy, control softwar and
precise heat delivery.
The go d news however is that these are areas in
which we specialize—making us a leader in pipe
weld-seam normalizing. Also, with more than 50
years’ induction heating experience, we’re experts at
using technology to open new commercial opportu-
nities f r our customers.
EFD Ind cti n is E rope’s o 1—and th world’s
no. 2—inducti n company. Our sy tems re used to
weld, normalize, anneal, harden, t mper, braze,
melt, forge, bond, cure and pre- and post-heat.
So whatever your pipe normalizing needs, you
can tu to us for a sol tion. And since we’re p esent
around the world, that solution s probably closer
than you think. Contact us today. There’s a vast oil
and gas pipe market out there. We’ll help you get a
share of it.
Learn more about our pipe welding and normaliz-
ing solutions at Fabtech 2011—visit us at Booth 348.