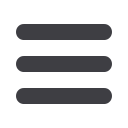

S
eptember
2011
91
›
T
echnology
U
pdate
Dr. Linsinger-Str. 24, A-4662 Steyrermuehl
Tel. +43 7613 88 40, Fax +43 7613 88 40-951
E-Mail:
maschinenbau@linsinger.comw w w. l i n s i n g e r . c o m
The new Generation of
Carbide Circular Sawing Machines
Cutting of
steel billets
up to 800 mm
diameter
KSA 2200 DPD – World largest
Carbide Circular Sawing Machine
Saw blade Diameter 2200 mm
Equipped with the patented
LINSINGER
LINCUT® technology and
LINSINGER
DPD gearbox.
PEAK AIM
3000 MM DIAMETER
SAW BLADE
Tube-and-Pipe_180x125_07-2011.indd 1
21.07.2011 15:02
Optimised
processes
for tube
bending
and forming
TRANSFLUID Maschinenbau GmbH
develops free-of-interface automation systems
from a single source, and ensures the optimal
set-up for the whole tube processing.
At the beginning of each transfluid
solution there are specific requirements.
“In this concrete case aluminium tubes of
17 x 1mm diameter were to be bent in a
bending radius of 10mm (0.58 x D),” said
Gerd Nöker, one of transfluid’s CEOs.
“The wall thinning on the exterior bend was
permitted a maximum of 30%. Additional
requirements were the possibility for a
bend sequence with various radii, end
forming on both ends and a cycle time of
maximal 15 seconds per component with
up to six bends.”
To speed up the tube bending process
and at the same time reduce handling
costs, transfluid developed a solution
that forms one side of the aluminium
tube before bending. After that, a 4-axle
handling system takes over loading the
fully electric transfluid bending machine.
The safe inward transfer of the 80 to
800mm-long tubes is guaranteed by
loading from a step feeding system with a
capacity up to 500 workpieces.
To ensure optimal quality upon
bending, the length of every tube is exactly
checked before feeding. The bent tubes
are then removed by a robot and fed into
a combined transfluid forming machine. In
one step, the chipless cutting of overlength
takes place as well as simultaneous axial
forming. Subsequently, the robot feeds the
single tubes to an optical measurement to
completely control the forming geometries
and surfaces.
The integrated transfluid automation
system (t motion) can also process very
short parts that, on customer request, are to
be end-formed on both ends after bending.
For this, the forming machine is equipped
with an automatic clamping jaw changer.
This allows quick changing between two
different form clamping pieces, according to
requirements.
transfluid Maschinenbau GmbH
–
Germany
Fax: +49 2972 9715 11
Email:
info@transfluid.deWebsite:
www.transfluid.deFrom a single
source to a bent
and formed tube,
even with very small
bending radii