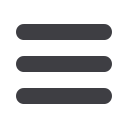

news
Wire & Cable ASIA – May/June 2009
34
William Hughes Ltd specialises in
making complex wire components and
was recently asked to manufacture a
threaded linkhook with many bends,
for use in the diesel pumps used in
lorries and cars. The small component
is formed from a piece of wire just
117.4mm long and has to meet precise
dimensional tolerances.
Based on a 2.6mm diameter length of
annealed steel wire, the component
passes through five different processes
before it is ready for use. The first
stage is to form a hook at one end and
a chamfer on the other using a rotary
table, six-stage blanking machine. The
partly formed component then moves
to a thread cutting machine where a
20mm long thread (4 x 40 UNC) is cut
on the chamfered end.
The partly formed linkhook is then
subject to a press bend and two hand
bends to form the precise shape
required before being case hardened
in a special sealed quenched furnace.
The components are then checked
for accuracy to the correct dimen-
sions and specification using high
technology inspection equipment.
William Hughes has been making bent
wire components and springs for over
200 years and continues to expand
its range of products, processes and
finishes which now include shot
peening, and the Delta
®
Tone and
Delta
®
Seal coating processes. The
company also offers an electrophoretic
paint process, which provides the
black, gloss finish popular in the
automotive industry.
William Hughes has the technical
resources to help its customers design
and manufacture a range of bent wire
components, as well as helping to
solve a wide range of engineering and
design challenges. A rapid design and
prototyping service is available for wire
products including springs and bent
wire components. Quality systems to
ISO 9001:2000, ISO/TS16949: 2002,
the latest automotive standard and
AS9100 for aerospace ensure
consistency and accuracy of supply.
William Hughes Ltd – UK
Fax
: +44 1963 363377
:
sales@wmhughes.co.ukWebsite
:
www.wmhughes.co.ukComponents from wire
ECC 701 coating systems from
Nordson Corporation provide precise
process control for applying powders
for high quality, reproducible cable
coating. The system maintains an
even flow of powder to consistently
produce the desired coating thick-
ness. The new dual-filter system and
improved pump technology help
reduce
material
usage,
lower
production costs and allow handling
of abrasive materials.
ECC 701 systems fluidise and charge
various powders, including talcs and
superabsorbent powders (SAPs), to
spray on to cable.
The systems precisely control all
process parameters for repeatable
coating, and parameters can be easily
adjusted to meet changing application
requirements.
Use of Versa-Spray
®
guns optimises
performance of various powders using
the corona process to charge powder
particles. Versatile, industry-proven
Versa-Spray guns process a wide
variety of materials from talcs to
abrasive substances such as SAPs.
The new dual-filter system recovers
material not applied to cables and
returns it to the hopper.
This results in high transfer efficiency
while also providing a clean produc-
tion environment. The modular system
design has flexible inputs and out-
puts for easy integration into existing
production lines.
Nordson Corporation – USA
Website
:
www.nordson.comPowder handling for coating systems
Direct electrical
heating system for
subsea installation
Nexans has been awarded an €11
million contract by BP Norge to
supply a direct electrical heating
(DEH) system for the Skarv field
subsea production pipeline in the
Norwegian Sea. Nexans is believed
to be the only supplier with
experience of this technology and
has already supplied this type of
system for 17 subsea pipeline
installations.
A number of methods may be used
for maintaining flow, such as
chemical injection, but DEH has
proved to be both a reliable and
eco-friendly solution to the
problem.
Nexans will supply all cables and
dedicated subsea equipment for
the DEH system. The cables will be
manufactured at Nexans’ Halden
factory in Norway and are
scheduled for delivery in the spring
of 2010.
Nexans – France
Fax
: +33 15669 8484
:
nexans.web@nexans.comWebsite
:
www.nexans.com❍
Linkhook for a diesel pump
❍
Handling system, ECC 701