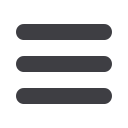

•
Improved safety: There is
no arcing, which is a major plus in
hazardous environments such as gas-
filled chambers.
•
Cost savings: There is no wear
and tear thus improving the uptime and
reducing maintenance.
However, a truly contactless connector
must be able to transmit both data and
power. For power, there are few options.
Capacitive power transfer (CPT) has the
advantage of being able to penetrate
(floating) metal and has low EMI, but it
suffers from low power density and short
range. Some generalized comparisons
of various wireless options, using pros
and cons, are shown for easy reference
(Figure 1.)
For contactless power transfer, an
inductively coupled power transfer
(ICPT) option proves to have more
pros than cons. It is has high power
density at reasonable distance, is well
known with widely available product
and technology solutions, and high
efficiency is possible. The downside is
that it cannot penetrate metal.
For data transmission, there are a
number of options. Capacitive coupling’s
low EMI is also an advantage for data
transfer, but such coupling requires
significant surface-plate area, which
can be challenging for tiny, rotating
couplers. Inductive coupling for data
suffers from low bit rates. Other options
include RF at 60 GHz, 2.45 or 5 GHz,
sub-GHz, and ICPT, as well as optical
links. Each has pros and cons, as shown
in Figure 1.
The 2.45-GHz industrial, scientific,
medical (ISM) band is also unlicensed,
with global acceptance and wide usage,
most notably as “wireless Ethernet”
under the moniker of Wi-Fi.
In the final analysis, it turns out that
a hybrid architecture, RF for data and
inductive coupling for power, is the best
approach for contactless connectivity.
Defining induction
Inductive power transfer has been with
us for quite some time, but for the sake
of clarity a quick run through of how
it works is useful in understanding its
utility as a wireless power-transfer
mechanism.
Faraday's law of induction states that
the induced electromotive force in any
closed circuit is equal to the rate of
change of the magnetic flux enclosed
by the circuit, or mathematically as:
Where is the electromotive force (EMF)
and ΦB is the magnetic flux.
The basic principle of an inductively
coupled power-transfer system is
shown (Figure 2). It consists of a
transmitter coil L1 and a receiver
coil L2. Both coils form a system of
magnetically coupled inductors. An
alternating current in the transmitter
coil generates a magnetic field, which
induces a voltage in the receiver coil.
The efficiency of the power transfer
depends on the coupling (k) between
the inductors and their quality, defined
as their Q factor.
The coupling is determined by the
distance between the inductors (z) and
the ratio of D2/D. The shape of the coils
and the angle between them further
determines the effective coupling.
The performance of a wireless power
link can be improved using resonant
inductive coupling. Resonance of
a circuit involving capacitors and
inductors occurs because the collapsing
magnetic field of the inductor generates
an electric current in its windings that
charges the capacitor, and then the
discharging capacitor provides an
electric current that builds the magnetic
field in the inductor. This process is
repeated continually.
At resonance, the series impedance of
the two elements is at a minimum and
the parallel impedance is at maximum.
Resonance is used for tuning and
filtering, because it occurs at a
particular frequency for given values of
inductance and capacitance.
To cancel the influence of the inductive
reactance and the capacitive reactance
they should have equal magnitude, ωL
= 1/ωC, so:
Where L is the inductance in Henrys,
C is the capacitance in Farads , and
ω = 2πf, in which f is the resonance
frequency in Hertz. In low-power
systems and for high power efficiency,
higher k and Q are required.
Figure 6: Free from the strictures of contact, contactless
interconnects provide greatly improved flexibility and reliability,
while magnetic coupling protects against explosions in gaseous or
otherwise flammable environments.
New-Tech Magazine Europe l 33