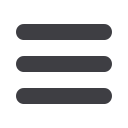

minimized. However, when receive
signals can be only 2 or 3% the
amplitude of transmit signals this
becomes mechanically very difficult
to accomplish when routing signals on
the same layer in the vicinity of the
connectors.
The third of these (skew or difference
in travel time in the two sides of a
differential pair), is a result of the
uneven distribution of the glass in
the woven cloth and the resin used
to bind the composite together. This
unevenness is due to the fact that the
glass bundles used to weave the cloth
are much larger than the width of the
traces. Figure 2 is a photo of a common
glass weave cloth (1080) with a 3.5 mil
(89 micron) wire superimposed on it to
show the difference in scale of traces
and glass weaves. Notice that for part
of the time the wire is on top of a
glass bundle with a dielectric constant
of about 6 and part of the time it is in
between glass bundles in pure resin
that has a dielectric constant of about
3. Signals will travel faster when they
are in pure resin than when they are
traveling over glass. This variation in
velocity is what causes differences
in travel time between the two sides
of a differential pair. We have seen
differences in travel time over 14 inch
(35 cm) differential pairs on 1080
glass as high as 62 ps. That is 60%
of a bit period at 10 Gb/s and two bit
periods at 32 Gb/s.
Many techniques have been proposed
to minimize the effect of skew. The
two most common methods in use
are:
• Routing the signals at an angle
to the glass weave hoping that the
irregularities are evened out between
the two sides of the pair.
• Using a glass weave style that
has the glass evenly spread out to
minimize variation in the glass weave
over which signals travel.
The first of these two methods has
taken two forms. One is to route the
signals in the PCB at an angle so that
when the PCB is fabricated the traces
run at an angle to the glass cloth
weave. This has proved impractical
in most products because the large
number of connector and component
pins impose an X-Y grid on routing.
Alternatively, the PCB or backplane
is routed on an X-Y orientation and
the artwork is placed at an angle on
the fabrication panel resulting in the
traces running at an angle to the
glass weave. This method wastes
substantial amounts of board material
Figure 3. 1067 glass weave and a 4 mil trace
Figure 4. Loss vs. Frequency of materials available for high speed
42 l New-Tech Magazine Europe