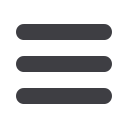

February 2017
•
MechChem Africa
¦
25
⎪
Corrosion control and coatings
⎪
Kansai Plascon
supervises bridge project in Lesotho
Kansai Plascon has provided an on site monitoring ser-
vice for a major bridge sandblasting project in Lesotho,
which also used specialist products from its Protective
Coatings division.
The project required sand blasting the steel bridge
surfaces to ISO 8501 1:2007 (Sa 2½). This was followed
by an application of a zinc rich epoxy primer and two
coats each of Plascotuff Epoxy MIO Intermediate Coat
and Plascothane 9000 Polyurethane Acrylic.
“Our on site monitoring of the application involved
spot checks on the surface preparation, aswell as dry film
thickness (DFT) readings,” explains Mike Byrd, national
protective coatings specification manager for Kansai
Plascon.
The company had technical specialists on site for the project. The Protective Coatings
division has had prior experience with bridge projects, which stood it in good stead in
clinching the Lesotho contract.
Byrd adds that the success achievedwith this particular project was also due toKansai
Plascon’s 360° guarantee system, which involves the end user, applicator and the coatings
manufacturer itself.
Plascotuff EpoxyMIOIntermediateCoat is a two component polyamide epoxy contain-
ingmicaceous (sparkling) iron oxide. It provides a high build barrier coating for protecting
steel in aggressive conditions, as well as an abrasion resistant coat for shop coated steel.
Plascothane 9000 Polyurethane Acrylic is a two component re-coatable polyurethane
acrylic highperformancefinish– formaintenance andnewconstruction–withanexcellent
decorative appearance. It features high gloss and colour retention, long term protection
and durability and is available in a range of colours. An added benefit is that a high DFT
thickness can be achieved with a single application.
q
compile reports onour findings, and thenpro-
vide corrosion-protection solutions specific
to each scenario,” Byrd explains. “We offer
a 360° guarantee, in addition to monitoring
all progress.”
Specialist coating products supplied to
this sector are Plascoline 1000 internal lin-
ing, Plascotuff 3000 primer, Plascotuff MIO
intermediate coating, and Plascothane 9000
topcoat. In addition, the Protective Coatings
divisionoffers technical and aftermarket sup-
port, as well as project management.
“We go to great lengths to support and
supply our customers, including newproduct
developments. Kansai Plascon has always
been at the forefront of coatings develop-
ment, as we expand our product range with
new technologies,” Byrd notes.
“Our custom-made solutions extend
the life of essential infrastructure in the
petrochemical industry by protecting tanks,
piping and structural steel from corrosion.
By keeping such infrastructure serviceable,
these operations run continuously, with
no costly stoppages and downtime, which
translates into constant production rates,”
Byrd concludes.
Turnkey coatings for the mining
industry
Despiteanongoingslumpintheminingsector,
KansaiPlasconhasmaintaineditscompetitive
edge as a leading paint supplier to the indus-
try, thanks to the fact that it offers a 360-de-
gree turnkey solution that is comprised of
decorative products, mine marking products
and protective coating products – all backed
by dedicated after-sales support.
Kansai Plascon is the market-leader in
supplying decorative coatings and aero-
sol marking paint to the mining industry.
Decorativepaint products areusedonmining
properties, which include staff houses, hos-
tels andoffices, whilemarking paints areused
at operational level in shafts. Kansai Plascon
brand manager for industrial coatings,
Mareta le Roux, says although the company
boasts majority market share in these areas,
there is still room for growth.
“One area of mining that holds consider-
able growth potential for us is corrosion pro-
tection for processing plants such as smelters
and concentrators. We are a relatively minor
player in this field at present. However, the
strategicfive-year plan in terms of resourcing,
is to put a focus on corrosion protection for
the inmine processing plants. Our protective
coating products meet all industry require-
ments, and it is now a matter of driving them
forward,” she states.
Over the years, Kansai Plascon has devel-
oped fundamentally strong relationshipswith
someof the largest names in theglobalmining
industry. Le Roux believes that this will work
to the company’s advantage, whenpromoting
its protective coating range. “This is already
bearing fruit, as a large goldmining operation
with mines in East, West and Central Africa
nowspecifies PlasconProtective coatings for
all of its processing plants.We have also been
supplying products to mines in the Zambian
copper belt for a number of years. Further
expansion in Africa holds the potential for
measurable growth.”
“We are by far the biggest coatings manu
facturer in Southern Africa, and we offer
a one-stop shopping experience that our
competitors cannot,” reveals Kansai Plascon
national market manager for mining and
mineralsandroadmarking,RolfRedelinghuys.
He adds that technical strengthand capability
also places Plascon ahead of the competition.
“Our service is not just selling protective
coatings, but doing specifications. We are
experts as far as that is concerned.We do not
just sell thepaint andwalkaway– there is sup-
port provided throughout the process. Our
technical teams undertake site visits to check
if the product is applied correctly, especially
when it comes to the corrosion protection,”
he elaborates.
Corrosion protection is expensive to ap-
ply and, le Roux indicates: “It is essential to
successfully complete the application of the
coating on the first attempt. Bearing this is
mind, we provide extensive training tomining
contractors at no additional charge. It’s all
about the customers’ bottom line at the end
of the day, and we are there to ensure that
everything goes according to plan.”
With regard to researchanddevelopment,
Kansai Plascon boasts a state-of-the-art
laboratory in Durban, KZN, which features
dedicated teams working solely on industrial
and protective coatings. “Our laboratory is
world-class, therefore, most of our research
and development is done locally, based on
local customer requirements,” says le Roux.
Kansai Plascon also boasts a strong net-
work of distributors in sub-Saharan African
regions such as Namibia, Botswana, Zambia,
Malawi, Zimbabwe and Mozambique, with
plans to expand the network in East Africa
andWest Africa. This networkwill enable the
company todeliver its rangeof products in the
quickest turnaround times.
In challenging economic times, the current
industry trend is to prioritise maintenance.
Redelinghuys believes that this works to
Kansai Plascon’s advantage. “Mining com-
panies are moving towards optimising and
conserving their assets, rather than replacing
them with new ones. As a result, our sector
sales have improved, and I am confident we
will gain market share in the foreseeable
future,” he concludes.
q