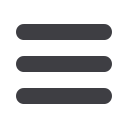

February 2017
•
MechChem Africa
¦
43
Thermoacoustic refrigeration
Thermoacoustic (TA) engines use a steep tem-
perature gradient to induce high-amplitude
sound waves and/or they use high-amplitude
sound waves to pump heat from one place to
another.
Thermalenergyappliedtotheprimemover
generates a temperature gradient along a
porous regenerator. At a specific temperature
gradient, self-sustained acoustic waves are
generated inside an acoustic resonator.
The acousticwave canbe used to generate
power via a piezoelectric diaphragm, placed
at the end of the resonator, which converts
the acoustic vibration directly into electrical
energy.
Also,though,theresonatingacousticvibra-
tions can be used to produce
a heat pump/refrigeration ef-
fect, via separate hot and cold
heat exchangers. Compared to
vapour refrigerators, thermoa-
coustic refrigerators have no
ozone-depleting or toxic cool-
ant and fewor nomovingparts.
They therefore require no
dynamic sealing or lubrication.
The technology is also very
attractivebecause of its simple
low-cost construction, low
maintenance cost and envi-
ronmental friendliness. These systems also
have the potential to utilise low-quality heat
sourcessuchasindustrialwasteheat,solaren-
ergy or flue gases fromcombustion processes
for energy recovery.
From acoustics to cooling
Acoustic waves are longitudinal waves made
up of alternating high-pressure and low-pres-
sure zones. At a micro level, the temperature
of the gas in a high-pressure zone is raised,
while that in the lowpressure zone is lowered.
By locating these different zones precisely via
resonance, it is possible to use heat exchang-
ers to extract heat and to create increasingly
hot and cold temperature zones.
q
moving parts
A schematic representation of a thermoacoustic hot-air engine/
prime mover. The alternately hot and cold zones cause self-sustained
acoustic waves to be generated inside the acoustic resonator.
of the cooling power to the total input heating
power, that is, the sum of the heating power of
each engine.
Results
The COP increased as the temperature of
the heat exchangers in the primer loop was
increased and the maximum value of COP was
0.029 at 260 °C, with corresponding cooling
power of 35.6W.
Furthermore, the researchers obtained gas
oscillations at 85 °C – that is lower than the
boiling point of water – thereby opening up pos-
sibilities for applications of this technology for
refrigeration and power generation using low
temperature waste heat in factories and auto-
mobile engines. Also, refrigeration at -42.3 °C
was achieved using input heat at 90 °C.
Next steps
“The addition of multiple regenerators in the
vicinity of the ‘sweet spot’ of the prime mover
loop is a major advance in travelling-wave TA
engines,” says Hasegawa. “This configuration
⎪
Innovative engineering
⎪
reduces the temperature for TAoscillations and
improves cooling performance.”
Following the successful development of the
prototype thermoacoustic refrigerator system,
the next step in this research at Tokai University
is the development of practical TA engines with
a primary goal of contributing to overcoming
environmental problems.
q
References
1. Esmatullah Maiwand Sharify; Shinya
Hasegawa: Travelling-wave thermoacous-
tic refrigerator driven by a multistage
travelling-wave thermoacoustic engine:
Applied Thermal Engineering
, November
2016. DOI:
http://dx.doi.org/10.1016/j.applthermaleng.2016.11.021
2. Mariko Senga; Shinya Hasegawa: Design and
experimental verification of a cascade wave-
wave thermoacoustic amplifier:
Journal of
Applied Physics
(JAP), 119, 204906 (2016).
DOI:
http://dx.doi.org/10.1063/1.49529833. ShinyaHasegawawebsite(inJapanese)http://
www.ed.u-tokai.ac.jp/thermoacoustic/index.html
4. Video, Thermoacoustic refrigerator. http://
www.ed.u-tokai.ac.jp/thermoacoustic/VIDEO.zip Password: thermoacoustic.