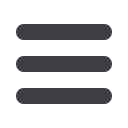

April 2015
MODERN MINING
7
MINING News
Ore loading in the Wassa main pit (photo: GSR).
underground life and will remove the
requirement for a raisebore ventilation
raise and escape way close to the start of
the decline. The main decline will be 5,8 m
high and 5,2 mwide and will be developed
using standard trackless mechanised min-
ing methods.
The upper stopes will be mined using
longitudinal longhole open stoping with
waste rock fill. This will enable efficient
early production before a cemented rock
fill preparation and delivery system is
installed. The open pit will eventually mine
down to the top of these upper stopes, but
only towards the end of the life of mine.
In the deeper, wider areas of the deposit
a transverse longhole open stoping
method will be used. A primary-secondary
mining sequence will be implemented
with the primary stopes filled with
cemented rock fill and the secondary
stopes with waste rock fill. The overall stop-
ing sequence will be bottom-up to reduce
the incidence of sill pillar development.
New surface infrastructure to support
the underground mining will be con-
structed including electrical power supply
from the grid with backup genset support
and surface mechanical and electrical
workshops.
At steady state production, the Wassa
Underground is expected to produce an
average of approximately 2 000 tonnes per
day across the life of mine.
GSR holds a 90 % interest in the Wassa,
Prestea and Bogoso gold mines in Ghana.
In 2014, the company produced 261 000
ounces of gold.
Leach processing selected for Kabwe pilot plant
London-based Berkeley Mineral Resources
(BMR) announced on 11 December 2014
that it was undertaking a peer review of the
definitive feasibility study (DFS) for process-
ing the washplant tailings (WPT) at Kabwe
in Zambia
The company subsequently reported on
2 February 2015 that related test work on
theWPT was well advanced and that prelim-
inary metallurgical and mineralogical test
work was about to start on the leach plant
residue (LPR) tailings at Kabwe, the compa-
ny’s largest JORC-compliant resource.
Dr Geoff Casson, the GM of the compa-
ny’s Zambian operations, was in attendance
throughout the test work referred to above.
In the light of his findings, BMR says it has
now selected a leach processing method-
ology for the pilot plant processing of the
WPT and LPR.
BMR arranged for a 5-t sample of WPT
to be subjected to a full multi-spiral, gravity
separationpilot test by spiral process special-
ists in South Africa to establish the potential
recovery and grade of zinc and lead under
simulated plant operating conditions.
Notwithstanding BMR’s initial prefer-
ence for multi-spiral gravity separation,
the results of this test work ultimately did
not replicate either the potential recov-
eries or grades of the zinc and lead in
the final product claimed in the DFS, and
metal recoveries were materially inferior
to those reported in the DFS. In summary,
the volume of fine material generated after
scrubbing exceeded 50 % of the ore feed,
which proved untreatable by multi-spiral
gravity separation.
The alternative multi-gravity separation
technology proposed in the DFS, which is
often better suited to fine material, was also
considered. BMR, after carefully examining
previous test work results and taking into
account the high proportion of finer feed,
rejected this technology as impractical
and more costly, without offering a com-
mensurate improvement in zinc and lead
recoveries.
A further attempt to improve zinc and
lead recoveries by pre-treating the spi-
ral feed was undertaken using Wet High
Intensity Magnetic Separation. The objec-
tive was to reduce the high percentage
of iron (ferrite) competing with the zinc.
Whilst some iron was removed, the losses
of zinc and lead, locked within the iron
minerals was unacceptable and led to low
recoveries of both.
Says BMR: “The Directors therefore
concluded that the DFS, which had been
commissioned in August 2013 and the
results of which were accepted without
sufficient challenge by the former Board
chaired by Masoud Alikhani, does not pro-
vide an acceptable basis for selecting an
appropriate processing methodology for
the Kabwe tailings.
“Furthermore, the Directors resolved
… not to pursue gravity separation as a
potential methodology for metal recovery
and the DFS has been removed from the
company’s website.”
BMR says the metallurgical and mineral-
ogical test work on the LPR tailings using
leach processing, which was resurrected
by the new Board earlier this year, has now
advanced to mini-pilot stage.
It adds that this proprietary process,
which is being developed by BMR working
with technical partners, provides a credible
alternative for the recovery of zinc and lead
from both theWPT and LPR tailings. Results
to date are encouraging in that the zinc
and lead recoveries achieved are approxi-
mately 55 % and 85 % respectively, each of
which represents an improvement on the
previously claimed recoveries from grav-
ity processing in the DFS. Furthermore, the
process generates no toxic effluents.
BMR says it expects to finalise the design
parameters for a pilot plant in the next few
weeks.