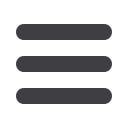

CAPITAL EQUIPMENT NEWS
JUNE 2017
32
Babcock’s equipment division will be
delivering 19 new Volvo machines to
Stefanutti Stocks Mining Services (SSMS)
in a sales agreement that is not only
noteworthy for its size, but also as it’s
the first time the leading construction
consortium will be utilising Volvo
construction equipment.
Mark Barrett, sales representative
at Babcock’s equipment division, says
Babcock’s contract comprises the delivery
of 15 A40G dump trucks and four EC750
crawler excavators for a new open pit
coal mining project outside Ermelo. The
agreement also includes a 5 000-hour
service contract from Babcock.
Stefanutti Stocks’ mining operations
include drilling explorations, blasting
and load and haul of the various material
types, and the Volvo machines are needed
to meet monthly production targets on the
mine. The Volvo A40G articulated haulers,
with their 39 000 kg payload, will be used
to transport the coal from the pit, while the
EC750D excavators with their increased
bucket capacity and greater digging force,
will be used to load the A40Gs.
Freddie Strydom, Stefanutti Stocks
Mining Services contracts director, says
price, reliability, aftermarket service,
availability of spare parts and cost of spare
parts all played a role in the final decision
to purchase Volvo construction equipment
from Babcock.
Babcock is the exclusive regional dis-
tributor of Volvo construction equipment
in southern Africa and is well-estab-
lished as one of Africa’s industry leaders
in building long-term relationships with
its customers. Barrett believes that this,
together with Babcock’s competitive
pricing and strong reputation of the Vol-
vo brand, gave the company an edge over
competitors.
The open pit coal mining project outside
of Ermelo has an estimated life span of
eight years over which approximately 10,1
million tonnes of coal and 53,6 million
Stefanutti Stocks opts for Volvo gear
MINING NEWS
With an industry target set to eliminate mining
fatalities by 2020 and reduce Lost Time Injuries
by 20% from January 2017, the pressure is on
mines and their suppliers, including those in
the field of proximity detection systems (PDS),
to meet this vital goal.
“Transport-related incidents are still one
of the top causes of fatalities, alongside
fall-of-ground,” says Anton Lourens, MD
of Booyco Electronics, a leading PDS OEM.
“While deaths in mining fell 5% to a record
low of 73 in 2016 and injuries fell 15% to
2 662 last year, there is still a long way to go
to meet the 2020 target.”
Lourens says PDS is a key part of the sector’s
strategy to implement zero harm, and is already
a legislated requirement for underground coal
mines, who need to ensure their systems are
‘fit for purpose’ in order to comply.
“Coal mines continue to make strides
towards better safety, with the injury rate in
2016 down 11% to 183 from 206 in 2015,” he
says. “Continued progress requires ongoing
compliance and dedication to implementing
not just the later but the spirit of the law.”
PDS allows for interventions where
a potentially dangerous situation exists
between a pedestrian and a machine. The
system includes a sensing device, to detect
the presence of an object in a working area,
and an audible and visual alarm to both
the equipment operator and pedestrians as
they enter danger zones. It can also help
locate people and machinery if there is an
emergency underground.
Apart from the safety aspect, the
technology helps mines to locate pedestrians
and vehicles underground, providing data
that can be analysed for patterns that affect
production efficiencies.
“The groundwork for the wider application
of PDS has already been laid down by the
Department of Mineral Resources, through an
amendment to Chapter 8 of the Mines Health
and Safety Act (MHSA) in February 2015,” he
says. “It is now required that PDS be installed
on all mobile equipment on mines.”
He highlights that mines are required to
assess significant risk in terms of moving
machinery and people, and to put an action
plan in place to mitigate that risk. One of the
challenges, however, is that some mines still
consider PDS a ‘grudge purchase’, and do not
fully understand their legal responsibility to
choose suppliers whose equipment is fit-for-
purpose.
“While it may be tempting for a mine to
select the cheapest equipment, they will
need to prove in the case of an inspection
or an accident that the equipment is up to
the task and compliant,” says Lourens. “Even
from our point of view as PDS suppliers,
we have a legal responsibility to deliver a
reliable solution, as suppliers can also be
legally charged if the equipment fails to
comply.”
b
bank cubic metres of waste material will
be moved.
Stefanutti Stocks is a leading multidisci-
plinary construction group operating across
southern Africa, Africa and the Middle
East. Its mining portfolio includes the de-
sign and construction of mine infrastruc-
ture, open pit mine design and scheduling,
open pit mining, materials handling and
tailings operations with the capability to
construct the full spectrum of mine infra-
structure.
b
PDS can help meet zero fatality targets in
coal mines
Trysome renews collaboration
with Hexagon Mining
Trysome Auto Electrical South Africa has
announced the renewal of its reseller agreement
with Hexagon Mining. CEO, Eddie Smith and
Hexagon Mining President, Hélio Samora
strengthened the long-standing collaboration
between the organisations by signing a
new agreement at Trysome’s head office in
Johannesburg, South Africa, on April 21.
The partnership ensures the continued
availability of Hexagon Mining’s SAFEmine
suite of collision avoidance solutions in
the South African market. It also means
strengthened service and support for Hexagon
Mining’s wider portfolio of integrated
solutions. Besides collision avoidance and
fatigue monitoring, the solutions include
proven technologies for surveying, design, fleet
management and production optimisation.
Trysome has represented Hexagon Mining
in the sub-Saharan African region since 2008.
Today, the Collision Avoidance System (CAS)
is running in more than 25 000 mining vehicles
in more than 60 mines worldwide. Samora
and Smith agreed that renewed collaboration
is good news for customers in South Africa.
“Deadlines are looming for many mines
to comply with South Africa’s new safety
regulations, so this is a timely agreement
between our companies,” says Samora. “CAS
and our new Vehicle Intervention System
(VIS) will help customers protect their people
and equipment, as well as meeting those
deadlines.”
b