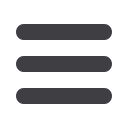

June 2017
AFRICAN FUSION
23
3D printing using CMT
A
mong the demonstrations of
Fronius welding equipment tak-
ing place on theBED standat MTA
this year, was a Kuka robot programmed
to create 3D-printed metal vases using
Fronius’ coldmetal transfer (CMT) weld-
ing process.
“While what we are doing here is
an ‘eye catcher’, it demonstrates a very
real metal-printing capability. We are
making vases in interesting shapes by
building up 204 layers of CMT-deposited
weld runs on top of one another,” says
Hiesmayr.
“But globally, we now have indus-
trial customers using the process to
manufacture complex components and
shapes such as propellers and wind
tower blades,” he adds.
The process can be done with any
industrial robot capable of manipulat-
ing a CMT welding torch. Welding starts
on a flat metal sheet, but no complex
moving bed is required. The shape is
simply programmed into the robot and,
because the CMT process is relatively
cold, the welding can often be done as
a continuous layer-on-layer process.
“Whenmilling intricate shapes such
as lattice structures where material has
to be removed for lightweighting, 80 to
90% of the expensive base materials is
wasted. Modern 3D printing techniques
puts the materials exactly where they
are needed, minimising waste and its
associated cost,” says Hiesmayr.
Most metal 3D printing systems are
complex and expensive, based on laser
sintering usingmachine beds that index
downwards during the build. The CMT
process with a robot, while not nearly
as accurate, enables a rough shape to
be established at a much lower cost.
This can then be final-machined – to the
accuracy and finish required – quickly
and with minimal material loss.
“Cranfield Institute of Technology
in the UK, for example, is using our CMT
processwith ABB robots tomanufacture
titaniumcomponents for the aerospace
3D printing
enabled by
Fronius’ CMT
At the BED stand at Machine Tools Africa (MTA), which
was held during May 2017, Fronius demonstrated the
3D-printing/additivemanufacturing capability of its CMT
welding process.
African Fusion
talks to BED’s welding
product manager, Craig Bister, and Thomas Hiermayr,
Fronius’ sales manager for the Middle East and Africa.
industry – andconfidence in the technol-
ogy is developing quickly,” Hiesemayr
tells
African Fusion
. “These are real
components that are machined after
3D-printed and then ready for use in
aircraft,” he says, adding that quantities
fromone-offs to production runs can be
accommodated.
“What you see here is just the begin-
ning. 3D printing and additivemanufac-
turing are part of amodern trend that is
here to stay and we are actively looking
for opportunities. All that is needed to
get started is a Fronius welding system
with a CMT capability and a small robot.
We believe this could be the most cost-
effective way to adopt this new manu-
facturing trend,” Hiemayr suggests.
Also on show was the new Fronius
TPSi MIG welding system, which is now
CMT ready. “A CMT module can be add-
ed, alongwith the CMT pull torchwith its
wire buffer, to add full CMT functionality
to the system,” continues Bister.
“These machines are excellent for
engineering companies, fabricators and
welded component manufacturers,” he
says. “With an array of modern features
such as pulsemulti control, penetration
stabiliser, arc length correction and the
modern digital displays and input con-
At Machine Tools Africa 2017, an industrial robot and Fronius’ CMT welding process was demonstrated
manufacturing a 3D-printed steel vase.
trols, Fronius’ TPSi offers unparalleled
welding performance. After a short basic
training session, most welders are easily
able to manage the machine and they
quickly come to enjoy its unique feel,”
Bister adds.
He adds that the new Fronius TPS
270i MIG/MAG machine has also now
become very popular with automotive
panel beaters that are now having to
do more and more aluminium welding.
“Fronius is very strong in the auto-
motive industry in South Africa. CMT has
been specified for the manufacture of
the new BMW XT line, with production
starting in October this year, and for
component suppliers such as Benteller,
which nowhas a total of 22 Fronius CMT
Advanced systems spread between
its PE and Alrode South plants,” he
concludes.