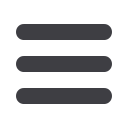

Technology News
www.read-tpt.com38
J
anuary
2015
Reducing the programming and
teach-time of welding processes
PROBLEMS can arise when switching
a production-line: during the switch
production stands still and sometimes
it takes even more time to reconfigure
and recalibrate than to actually switch
the tools. Even after the adjustments are
made the user still has to make sure that
the change of products fits the quality
criteria, which costs time and money.
The solution to this problem is online
seam-tracking sensors. This kind
of optical sensor can automatically
detect and compensate variations in
the geometry of parts and therefore
significantly reduce switching costs. If
any common robot is used for welding
processes, than a stand-alone sensor
like the TH6D from Scansonic MI GmbH
can easily be integrated into production.
It stores unlimited different welding
jobs and in combination with its online
detection, switching from one product to
another is simple.
The sensor uses triangulation for a
no-contact scan of the shape of the
seam at the joint. It then transmits the
current seam position to the control unit
of the robot. Based on the submitted
values, the robot can compensate
tolerances in Y (lateral displacement
along path) and Z (vertical offset along
path), without changing the existing
programming. The sensor has a very
sturdy construction. The optical filter to
prevent extraneous light helps to ensure
that operations proceed properly when
working less than 15mm to the process.
Reliable seam tracking is supported
by a powerful signal analysis feature,
which is especially useful on reflective
surfaces. The TH6D uses a state of
the art CMOS active pixel sensor to
get the most accruable measurements
possible.
If a welding robot is not used for
production it is still possible to lower
switching costs with the Scansonic MI
GmbHAuto-Guide system. It is an easy-
to-use plug and play system consisting
of the TH6D sensor in combination with
two linear axes. The system is supplied
ready to use and all components can
communicate with each other directly
after the mounting and without any
additional programming required. The
Auto-Guide system offers process
safety and reliability of a robot welding
and simplicity in the operating process.
Scansonic MI GmbH
– Germany
Website:
www.scansonic.deTungsten carbide-tipped saw blades
NEW-Form Tools has added tungsten
carbide tipped (TCT) circular saw
blades to its metal cutting product line.
Each blade is manufactured to reduce
downtime and increase operational
speed, and the TCT circular saw
blades are specifically designed to
address the specifications of the tube
and pipe industry.
The advanced blades can be used
for all kinds of metal cutting, producing
a burr-free cut through steel materials.
The carbide-tipped saw blades are
coated to last longer and it is claimed
that, in some cases, they can last four to
ten times longer than the average HSS
circular saw blade.
“Users will quickly see increased
sawing performance in their operation,”
said Tyler Jantzi, sales director for New-
Form Tools. “With advanced coatings,
our blades allow for the cleanest,
dependable cuts with less change-outs,
for overall higher productivity.”
The TCT circular saw blades also
work on a variety of sawing applications,
and can be re-sharpened by New-Form
Tools.
New-Form Tools
– Canada
Fax: +1 519 272 1992
Email:
tjantzi@newformtools.comWebsite:
www.newformtools.comThe mounted TH6D
Stainless steel pipe production
SURAJ Ltd is a manufacturer and
exporter of stainless steel seamless
pipes, tubes and U-tubes in various
sizes, specifications and grades. The
company has a strong presence in the
global market, and serves more than 70
countries around the world.
The size range is 6 to 323.9mm OD,
with 0.8 to 25mm thickness. Pipes are
available up to 12m in length; tubes up
to 30m. Materials include all austenitic,
ferritic, Duplex and Super Duplex
stainless steels, and manufacturing is
carried out according to ASTM, ASME,
EN, NFA and JIS standards.
Suraj also holds certificates for
quality in accordance with AD2000
Merkblatt W0 and Pressure Equipment
Directives 97/23/EC from TUV Nord,
and supplies products under all national
and international third party inspection
authorities.
Suraj Ltd
– India
Fax: +91 79 2754 0722
Email:
suraj@surajgroup.comWebsite:
www.surajgroup.com