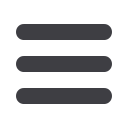

Industry News
www.read-tpt.com6
J
anuary
2015
Competence centres for the
tube industry
LINSINGER places emphasis on in-
house technology sourcing, and its
established Competence Centers for
sawing, milling and rail-milling provide
significant
contributions
towards
the company’s market growth. This
concentration of engineering know-how
is a foundation for ambitious projects in
all regions of the world.
Contrary to the general trend towards
securing profitability by restructuring the
workforce and relying on outsourcing,
Linsinger has improved its productivity,
quality and completion date reliability by
focusing on the competence of its own
in-house workforce.
Linsinger’s purchase of Wagner
Saws (formerly the world’s largest
sawing machine manufacturer) and the
resulting know-how was the starting
point for development of the Sawing
Competence Center. Consequently,
the company’s infrastructure was
extended with new production facilities
and the latest machine tooling. The
target was to assemble and test all
machines completely at Linsinger’s site.
Engineering, production services, quality
assurance and logistics management
are all available at the company’s own
manufacturing facility, and experienced
Linsinger engineers are permanently
on-call worldwide to work in partnership
with global customers to ensure
satisfaction and protect investments.
Both the Linsinger KSA tube layer saw
and the RTM pipe cutting machine have
been developed taking into account the
latest findings of vibration technology,
and create burr-free cuts suitable for
end-users without the need for additional
de-burring. The vortex milling process
of the RTM pipe cutting machine works
with many tool inserts orbiting around
the pipe. The number of cutters depends
on the diameter and wall thickness,
resulting in manageable short chips and
practically burr-free cuts.
The machines are designed for
heavy-duty three-shift operation, and
are characterised by high material
throughput. Linsinger supplies complete
turnkey equipment concepts, with all
necessary transport systems, and length
measurement stops for head, foot and
partial cuts, either single or in layers.
Turnkey systems including integration
and implementation in existing finishing
lines are also provided.
The Multi-Cut saw is equipped with up
to four axis-controlled sawing stations
working independently. Sawing of the
tube starts simultaneously at several
positions, and segments are finally
cut along its circumference. Small,
disposable saw blades with a high
number of coated cutting teeth are
used for lower saw blade loading and
increased tool life. The result is small
chips and negligible burr.
Linsinger Maschinenbau GmbH
–
Austria
Fax: +43 7613 8840 951
Email:
maschinenbau@linsinger.comWebsite:
www.linsinger.comAnother success for Eurolls
EUROLLS states that increasing
numbers of customers in the tube
industry are applying its design
experience to improve the quality of their
products or to solve quality problems,
and that its reputation as a ‘problem
solving’ partner represents added value
on being a recognised, reliable tooling
supplier for the industry.
A number of important orders,
including project and design, were
secured by Eurolls during 2014. The
company has consolidated relationships
with customers around the world for
their new installations or implementation
of existing ones, for the supply of steel
and tungsten carbide rolls, mainly based
on Eurolls tooling design.
Eurolls SpA has been selected by
SMS Meer GmbH and its customer,
Huta Labedy in Poland, as their partner
for the supply of tooling for their new
12¾" mill according to SMS Meer GmbH
roll design.
Eurolls SpA
– Italy
Fax: +39 0432 796501
Website:
www.eurolls.comLarge-dimension roll