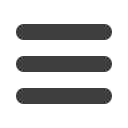

July 2013
22
www.read-eurowire.comEuroWire – January 2012
Maximum energy efficiency
▲
▲
ROEX Extruder generation
Technologynews
3
-eurowire.comRosendahl has been one of the leading
companies in extrusion lines for many
years. One of the biggest milestones
on the way towards this aim was the
continuous improvement which led to the
ROEX Extruder generation.
To achieve a reduction in power
consumption, Rosendahl focused on
the extruder unit (the main consumer
of energy in an extrusion line) and
developed measures to enhance the
energy efficiency of the new Rosendahl
Extruder generation ROEX.
The following improvements were made:
The drive has been modified from DC
technology to state-of-the-art A/C power
technology. Additionally the thyristor
rectifier which caused enormous wastage
due to reactive power was omitted.
By converting to a direct screw drive
by means of a planetary gear motor
mechanical losses were reduced. The
planetary gear is directly driven by four
symmetrically aligned motors (“compact
motor and gearbox design”).
Thanks to an optimised processing unit
(screw and feeding section) the material
output could be massively increased
while, at the same time, reducing energy
consumption.
During the development of the new
Extruder
generation
ROEX
special
attention was paid to additional electrical
power consumers like the heating and
cooling section. A new design of the
heating elements in combination with
the cooling channels and the fans allowed
substantially faster reactions of the
extruder temperature control.
The effect of this was not only a precise
control but also a reduction of the power
consumption of the heating and cooling
section.
Further machines of the Rosendahl
extrusion lines were subjected to
measures to increase efficiency.
It is of great importance to Rosendahl
that the latest technologies are constantly
applied (eg use of more efficient
electronic components like AC motors,
illuminants, conflation of several PLC
systems, regulators and relays).
Rosendahl also uses a high-level line
control system. This system coordinates
the processes of all machines and
demands only the power which is
required for each particular process.
Rosendahl’s ROEX Extruder generation
saves
compared
to
conventional
production lines from 15 to 25 per cent
energy for the entire production line with
a comparable productive capacity.
Rosendahl Maschinen GmbH – Austria
Website
:
www.rosendahlaustria.comNew single fusion splicer
Fujikura Europe has launched the 70S fusion splicer, replacing its FSM-60S core
alignment fusion splicer. The latest addition to Fujikura’s fusion splicer range, the
70S has been designed to be more ergonomic, faster and more durable than the
FSM-60S, reducing splicing time to just seven seconds.
A rugged construction design resists rain and dust, and will withstand a 30" drop
test on six sides. Two of the newest features include an automated wind protector
and a tube heater, developed for quicker splicing cycles and to reduce the number
of operational steps. The unit also includes a high-resolution LCD monitor,
powerful Li-ion battery and built-in training videos.
The 70S’s redesigned carry case can be used as a table for faster preparation for
mobile splicing, and a separate working table is included in the standard package.
This is the second fusion splicer launched this year by Fujikura, following the
release in February of the 12S.
Fujikura Europe – UK
Website
:
www.fujikura.co.uk