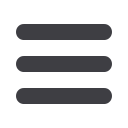

January 2017
MODERN MINING
65
COAL
of removing stones from coal – leading to the installation of a
number of sorting plants for de-stoning.
“But we wanted to go further,” he said. “We wanted to find
ways of upgrading our poor quality coal to meet Eskom speci-
fications, and we also wanted to explore the potential to scalp
off niche products from run-of-mine for the metallurgical sector
– most of which is currently imported.”
He said it was also fitting that Mintek should initiate this
research in partnership with another state-owned entity, as a
contribution to the national mandate of addressing energy secu-
rity for the country’s future.
Planning began six years ago, and testwork is now in its
fourth year. For the first couple of years, the testwork was
limited to laboratory testing at Mintek’s facility in Randburg.
According to McKenzie, this was very successful in showing
that different grades of coal could be distinguished, as the basis
of the upgrading process.
This was followed by the commissioning of a full-scale plant
for further testing, and SGS Bateman designed and built the
plant at Vlakfontein during 2016.
The application of the technology will differ depending on
the mine’s geology and location, according to Mintek Project
Specialist Isabel King.
“At Vlakfontein, for example, there is mining of the 4-Upper,
the 4-Lower and the 2 Seam, and each behaves differently in
the sorting process,” said King. “Some seams allow a high
grade product to be extracted, while others benefit more from
de-stoning; it’s really all about how you blend the final product
to achieve what you are after.”
She said the plant at Vlakfontein included a high-grade
sorter which concentrates the high-grade material, and a low-
grade sorter focused on removing stones.
“Our aim is to produce a range of coal products of relatively
high calorific value, ranging from about 21 to about 25 MJ per
kilogram – higher than Eskom’s requirements,” she said. The
results of the testing to date show that blending of low-grade
stockpiles will become very important – to enrich the poor
quality ore to power station standards.
“Some coal seams are unable to produce a high quality coal,
but could be upgraded to Eskom specifications,” said King.
“Some of the higher grade seams can produce a high quality
product when treated by this plant, and this could be blended
with the lower grade or waste stockpiles to meet Eskom’s stan-
dards. In fact, some of the high grade products could possibly
be sold at a premium to a different market.”
She said that while processing rates began at a moderate
pace, production has been ramped up and the plant can now
operate at full capacity.
“We believe that sensor-based sorting is the next step-chance
in the mineral processing sector,” said McKenzie. “Having this
full-scale plant actually on a mine site ensures that – as we put
the technology to the test – we have to confront and resolve all
the usual challenges and conditions that exist in mining, like
those related to water and electricity.”
He said the process was essentially based on a low water-
usage principle, and could substitute some of the older, more
conventional processes so that mines could reduce their water
footprint in the processing of coal.