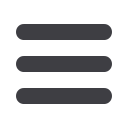

News
Corporate
March 2016
43
www.read-eurowire.comTenova’s expansion contract for Salzgitter
Salzgitter
Flachstahl
GmbH
has
awarded
Tenova
Metals
Germany
GmbH the contract for delivery of a
new secondary metallurgical unit at its
Salzgitter, Germany, plant. A new duplex
RH plant, used for the vacuum treatment
of liquid steel with a nominal heat size of
220 tons, will be designed and supplied.
The LD steelmaking shop of Salzgitter
Flachstahl produces about 4.7 million
tons of slabs per year. With the installation
of the new duplex RH plant, Salzgitter
Flachstahl will increase its production
volume of vacuum treated steel by another
two million tons per year. The main
purpose for the installation of the new
facilities is the production of automotive
steel grades (ultra low carbon IF steel), as
well as heavy plate grades.
For the execution of this project Tenova
undertakes the complete engineering,
supply of the entire mechanical and
electrical equipment, hardware, software,
installation and commissioning of the plant
equipment. The start of production of the
new plant is scheduled for spring 2017.
Steel production is carried out in three
LD converters, supplying liquid steel to
the secondary metallurgical facilities.
Therefore five lines (VPL1-5) with two
twin ladle furnaces and one additional
single ladle furnace completes the
secondary metallurgical facilities as they
are today. In three lines (VPL 1-3) VD
(vacuum degassing) plants are operated.
Subsequently, the refined liquid steel will
be cast by four slab casting machines.
The duplex RH plant consists of two
independent treatment stations, operated
with a hybrid steam jet pump system. Ladle
lifting is conducted by a winch system
for each station. Each treatment station is
also equipped with two ladle cars. After
receiving the liquid steel in the converter
bay the ladle will be transported to the RH
treatment station by ladle car“north”.
After treatment, the ladle will be received by
ladle car“south”and taken to the caster bay.
Depending
on
the
metallurgical
requirements, post vacuum treatment
will be carried out in the ladle treatment
station supplying metallurgical wires as
well as insulation powder addition.
Tenova Metals Germany GmbH –
Germany
Website
:
www.tenova.com▲
▲
The planned expansion being carried out by Tenova
Swager record?
Talurit AB’s latest swager, with a capacity of 4,200
tons, is the largest swager yet manufactured
by the company, and thought to be the largest
serial-made swager within the wire rope industry.
The 4,200-ton swager is the first in a series of
three machines commissioned from Talurit AB and
is bound for Kakogawa in Japan. The swager is
developed for making a mechanical splicing of an
eye on a wire rope with a diameter up to 152mm.
Wire rope swaged in these sizes is often used in the
offshore industry, when securing oil platforms.
Talurit AB delivers swagers of between 20 tons and
4,200 tons capacity to approximately 100 countries
around the world.
Talurit AB – Sweden
Website
:
www.talurit.se▲
▲
The new swager, thought to be the
largest one in the wire rope industry