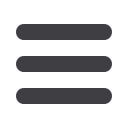

183
EuroWire – March 2008
wire
31 March-04 April
SMS Meer will be showcasing its wide
repertoire of products and services in plant
construction.
This ranges from integrated solutions,
including
mechanical,
electrical
and
automation systems, to high-performance
individual machines, as well as economical
modernisations.
Visitors will have the opportunity to take part
in discussions and multimedia presentations
so as to obtain an insight into plants and
process technologies from the areas of wire
rod mills.
In the field of wire rod mills the focus will
be on FRS® technology (Flexible Reduction
and Sizing) and CCT® cooling (Controlled
Cooling Technology), which have both
been developed by SMS Meer. They enable
efficient production of wire rod and ultra-fine
microstructure.
Furthermore, the visitors will also get to know
the restructured Service Central Department
of SMS Meer. With its vast product range and
concentrated expertise, the company offers
tailor-made service solutions to its customers
all around the globe, thereby ensuring the
high added value of the plants throughout
their life cycle.
SMS Meer GmbH – Germany
Fax
: +49 2161 350 883
:
info@sms-meer.comWebsite
:
www.sms-meer.comH A Schlatter, a manufacturer of compre-
hensive systems for the production of welded
wire mesh for reinforcing, industrial mesh,
wire products as well as plants to produce
woven wire mesh, will present innovative
solutions that increase profitability and
improve the production process by shorter
set-up times and an increased automation
degree.
A highly flexible plant type Superflex for the
production of standard and engineered wire
mesh will be on the stand.
This latest generation of the Superflex family
automatically aligns its compact welding
units to the dimension of the following mesh
type.
Also the adjustment of the cross wire feeder is
highly automated.
Also on display will be a welding plant
of System MG900 for the production of
industrial mesh. This is equipped with auto
adjusting components. A handling robot is
used for the stacking of the welded mesh
panels.
Potential customers can also find out
about the spare parts service, field service,
repair service, help desk performance and
training courses for efficient operation of
Schlatter plants.
The product range includes: Resistance
welding plants for reinforcing wire mesh,
System MG200 and System MG300; in-
dustrial wire mesh and fence mesh, System
MG600, System MG700 and System MG900;
flexible CNC-controlled welding centres,
System Posiweld; wire butt welders; wire
straightening and cutting devices and cold
rolling lines.
H A Schlatter AG – Switzerland
Fax
: +41 1 730 94 76
:
hans.balmer@schlatter.chWebsite
:
www.schlatter.chA new series of process monitoring terminals
for the metal forming industry will be the
highlight of the Schwer + Kopka stand.
The German process monitoring specialist
presents the new line as a complement to
its existing range of well proven compact
monitoring units.
All models offer fully automatic mode of
operation and are easy to operate. At the
same time, installation efforts are significantly
reduced.
The new series consists of three models
with different types of indicators and visual
displays. The base model SK 1-100 in fact has
completely eliminated all operational controls
and offers the highest possible quality
monitoring performance without any type of
operation or operator interference.
This ‘black box’type of system is accompanied
by two other models. The SK1-300 offers a
3.5" black and white touch screen, while the
SK 1-700 comprises a 7.5" full colour touch
screen display.
Both systems feature an entirely new
approach to visualising process data and to
communicating with the machine operator.
Rather than displaying an error message
when the machine is stopped due to a process
fault, or highlighting poor settings of the
monitoring parameters, the system suggests
remedial countermeasures and guides the
operator through possible improvements.
A second highlight will include the new
functions added to the company’s shop floor
data networking system SK-go!®. Among
these will be a new job scheduler which
allows to view on-line the work load on each
machine, and to re-schedule jobs by simple
drag-and-drop commands, and an expanded
module for documenting tool consumption.
Schwer & Kopka – Germany
Fax
: +49 751 47758
:
info@sk-gmbh.deWebsite
:
www.schwer-kopka.deSMS Meer
7A C21
H A Schlatter AG
11 A06
Schlatter’s welded wire mesh
▲
Schwer & Kopka GmbH
14 D02
Vital role in metal forming industry
▲