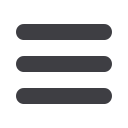

EuroWire – July 2010
43
Straightening, cutting & welding
First identified in 1724, cold pressure welding has many
advantages over electrical welding. The cold weld process is
faster, cleaner and more energy efficient, and creates a reliable,
permanent weld stronger than the parent material without
loss of electrical integrity. Cold welding is a form of solid
phase welding, unique because it is carried out at ambient
temperatures. Other types of solid phase welding, such as the
hammer welding of wrought iron carried out by blacksmiths for
centuries, are conducted at elevated temperatures. However,
although this involves high temperatures, the material is not
molten, merely more ductile.
How a weld is formed
There
have
been
several
explanations as to the actual
mechanism by which a cold
pressure weld is obtained.
For example, it has been
suggested that it happens
via recrystallisation or by an
energy hypothesis, but most
explanations have been either
experimentally disproved or
refuted on theoretical grounds.
The metallic bond
The currently accepted hypothesis relates to the fact that the
atoms of metals are held together by a metallic ‘bond’, so called
because it is peculiar to metallic substances. This bond can be
described as a ‘cloud’ of free negatively-charged electrons, which
envelop ionised positively charged atoms into a unit as a result of
attractive forces. So, if two metallic surfaces are brought together
with a space of only a few angstroms separation (there are
300 million angstroms to one centimetre), interaction between
the free electrons and ionised atoms can occur. This will
eliminate the potential barrier, allowing the electron cloud to
become common. This, in turn, effects a bond and therefore
a weld. A simpler way of explaining this process is to say that if
two surfaces (both atomically clean and atomically flat when
considered on an atomic scale) are put together, a bond is
effected equal to the parent metal. In practice, however,
bonding is virtually impossible under most conditions due to
surface irregularities, organic surface
contamination and chemical films such as
oxide films. In order to obtain maximum
weld efficiency, any form of contamination
must be reduced to a minimum, while the
area of contact has to be made as large as
possible.
Early attempts
In early applications of cold pressure butt
welding, the upset and radial displacement
of the interfaces was undertaken in a
single step. This was not very satisfactory,
since the ends to be joined had first to be
squared off and both surfaces had to be
free of contamination.
In addition, the amount of material
projecting from the gripping dies could
result in bending and lack of coaxiality, so
spoiling the correct flow of metal.
Multiple upset principle
A buttwelding system
employing
what
is
known as the ‘multiple
upset principle’ proved
more effective. When the
material is inserted in
the dies, each time the
machine is activated the
material is gripped by the
dies and fed forward.
As the two opposing faces
are forced against each
other, they are stretched
and enlarged over their
entire surface area.
This forces the oxides and
other surface impurities
outward from the core
of the material and
a
metallurgical
bond
stronger than the parent
material is effected. To ensure all impurities are forced out of
the interfaces, four to six ‘upsets’ are recommended.
Most non-ferrous metals can be cold welded as well as various
alloys. The cold weld process can also be used to join dissimilar
materials, for example, aluminium to copper, and materials of
different sizes.
High performance equipment
PWM Ltd designs and manufactures high performance cold
pressure welding machines and dies to suit a broad range of
applications, from hand-held, manually operated welders up to
electro-pneumatic and electro-hydraulic powered rod welders.
Precision engineered to provide consistent, reliable welds and
minimise materials wastage, PWM machines are very simple to
operate and easy to maintain.
PressureWelding Machines – UK Fax
: +44 1233 820591
:
pwm@btinternet.comWebsite
:
www.pwmltd.co.ukFlash photo
▲
▲
: Close up of an aluminium
weld showing the resulting flash where the
excess material, and any impurities, has
been squeezed out from the interfaces
Precision under pressure
Close-up weld
▲
▲
: Close up of a
cold weld on copper rod after
deflashing and rubbing down
ready for the drawing machine