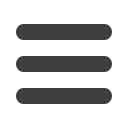

13
Chemical Technology • August 2016
Fibrous materials, such as hygienic wipes, have become
a major problem in waste water transport as their use has
markedly increased in the last few years. As a result of
the trend towards conserving drinking water and separat-
ing stormwater and waste water, the waste water to be
handled has become ‘thicker’. This is why operators now
demand non-clogging impellers that offer reliable operation
without sacrificing high efficiencies, even for small waste
water pumps.
Based on decades of experience in free-flow impeller
design, KSB’s hydraulic experts employed Computational
Fluid Dynamics (CFD) to gain detailed knowledge about the
complex flow processes inside the pump via computer-aided
simulations. The F-Max Impeller combines outstanding
hydraulics efficiency in a vortex impeller with the free pas-
sage of rigid and non-rigid solids through the pump. The
six vanes on the surface of the vortex impeller are spaced
at irregular intervals (Figure 2) that creates gaps which
allow rigid solids to pass through the impeller, even when
the impellers is close to the suction cover.
Machining grooves into the surface of the reverse side
of the impeller spread out from the centre balances
the axial thrust. Making a groove rather than a vane
means that the impeller can be moved closer to the
suction cover, thereby minimising the gap.
Having resolved the issue with rigid solids, KSB’s
designers turned their attention to that of soft tissues
and similar fibrous materials. Blockages involving soft ma-
terials start at the hub or ‘eye’ of the impeller and there is a
physical reason for this. The revolving motion of the impeller
introduces velocity and the greater the distance from the
centre of the impeller is where the velocity is greatest. If
there is material at the centre of the impeller, there is insuf-
ficient speed to eject the material which means that a swirl
has to be created to remove the material. The swirl comes
from the radius and shape inside the impeller vanes and
this swirl is three-dimensional and it is this which moves
the materials through the system.
The F-Max achieves a highly effective swirl motion
through a slight convex profile at the hub of the impel-
ler, achieving efficiencies that have previously only been
Figure 2: The six vanes on the surface of the vortex impeller
are spaced at irregular intervals.
PUMPS AND VALVES