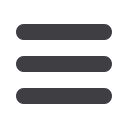

116
J
anuary
2012
www.read-tpt.com›
A
rticle
Improving standard methods of grain
size determination in high-alloy steel
and alloy products
D.Yu. Klyuev, Ye.Ya. Lezinskaya, V.V. Perchanik (National Metallurgical Academy of Ukraine)
N.A. Koryaka (ITA Representative in CIS, Ukraine)
Austenite or ferrite grain size is the major parameter of steel and
alloy single-phase structure. Determination of this parameter is
complicated by two reasons:
•
Opacity of the subject being measured
•
Imperfection of the methods used for grain size determination
Many methods for determination of metal grain structure parameters
appeared in the 20
th
century. They have made it possible to lay
down basic principles of a new trend in metal science: stereological
metallography. Stereometric Metallography by S.A. Saltykov,
Stereology in Physical Metallurgy by K.S. Cherniavsky, Quantitative
Microscopy by De Goff and Rines and Quantitative Stereology by
Underwood are fundamental works generalising the experience
gained in this direction during the last century.
Nearly a century-old history of existence of standard methods of
determination of grain size in steels and alloys underwent several
stages of its development. At first, methods of austenite and ferrite
grain identification were developed. American Society for Testing
and Materials (ASTM) pioneered creation of such standards.
In the early 1930s, ASTM Committee E4 developed a number of
standards including various methods of grain size determination
which formed the basis for analogous standards adopted in many
industrially developed countries, eg SIS 11 11 01 (Sweden), UNI
3245 (Italia), GOST 5639 (Russia), NF A04-102 (France), and SEP
1510 (Germany) which was transformed later into DIN 50601 and
ISO 643.
Methods in the above standards determine average dimensions
(diameter, area) or the number of the grains visible in a microsections
plane.
These methods are based on the development of reference
photographs with which structures seen in the microsections plane
are compared and the grain size is determined by the number of the
grains seen in one square inch at magnification ×100.
Grain size numbers have appeared much more later on, in standard
E112.
It is significant that evaluation by numbers was called forth by the
needs of metal product producers who had to control grain size in
their finished products. Introduction of conventional units (numbers)
has made much easier the grain size control operations but it
significantly worsened accuracy as compared with the quantitative
methods.
Nevertheless, all present-day standard methods of determination of
grain size in metals and alloys use exactly these conventional units.
All methods come to either visual comparison with photographic
references and expression in conventional units (numbers)
amounting from 18 (in GOST 5639) to 30 (in ASTM Е 112), or
counting the number of grains in a unit of length (chord method),
area or volume.
Chord method is of a lowest accuracy because of imperfect means
of determination of spatial dimensions and shapes of individual
crystallites in opaque materials of metal products. It does not ensure
a realistic view of such important parameters of a spatial structure
as grain anisotropy, shape, etc.
The existing methods developed for the reconstruction of spatial
structures by its flat layout in a metallographic section are rather
laborious and, again, coming to the determination of average
dimensions which does not allow establishment of the cause
of material property irregularities undoubtedly connected with
structural irregularities, ie grain anisotropy.
High-alloy steels and alloys used in high-duty structures (power
equipment, electronics, chemical equipment, space technology,
etc) are the materials the most prone to grain anisotropy. It should
be pointed out that the present-day methods of manufacture of
products form such materials, eg tubes for fuel element cans, allow
formation of a rather homogeneous structure in these products
[1-3]
.
At the same time, the available standard methods for evaluation of
such structures are rather imperfect. What concerns methods for
evaluation of grain anisotropy, they are practically absent.
Domain of above standards, except GOST 5639, spreads just to the
structures in which grain size distribution approaches the normal
one. And at the same time, if the image in the microsections plane is
closest to those in photographic references given in the standards,
the most trustworthy assessment results can be obtained. The
higher grain anisotropy of the structure, the higher is the error of its
assessment.