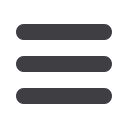

126
J
anuary
2012
www.read-tpt.com›
A
rticle
Manufacturers have tried to collar these pipe diameters despite
difficulties. This has led to great compromises because of the collar
quality. In short, as the pipe diameters get smaller and the wall
thickness in relation to pipe’s diameter grows, ie becomes thicker,
there are no working collaring methods (for branching) available.
Resulting from long development work of both collaring and
welding techniques, Larikka has developed a very clever solution
for manufacturing tubular parts like Tees where all the collaring
problems have been elegantly solved – no collaring at all. This
new solution is named Larikka CylinWeld and it approaches the
manufacturing these kind of “small” Tees and other pipe components
qualitatively and economically by welding cylindrical parts from
inside as its name reveals – cylinder internal welding. Due to this
innovative approach to the welding process all above mentioned
challenges in manufacturing tubular parts can be avoided.
Larikka CylinWeld –
the cylinder internal welding
The simplest approach to the mathematical pattern which the joining
surfaces of two hollow parts form is from inside and on the central
line of either tubular part. This kind of a mathematical pattern is easy
to control with current servo technics. Since the weldable parts must
be fixed together for the welding process and most commonly this
is made from outside the parts, the inside of the pipe parts remains
free for the welding process. Larikka CylinWeld is an application of
TIG-welding which cleverly utilises this vacant space inside of pipe
parts. In Larikka CylinWeld the electrode is directed inside the parts
to be welded either through the branch or the main pipe. Thus, the
welding takes place inside the tubular parts.
There are two significant things that happen when tubular parts are
welded from inside. Firstly, a round inner corner is formed as the
arc flame travels over the sharp inner corners of the tubular parts’
joining point and melts these corners. This kind of smooth and round
corner inside is flow-technically and in terms of material strength
a very good end result. Secondly, the root is on the part’s outer
surface making the visual check of weld’s full penetration easy.
The welding seams of Larikka
CylinWeld have undergone
both X-ray and pressure tests
with good results. X-ray test
results were class 5.
Also, the pressure
tests proved great
material strengths.
For
example,
a
3-branch manifold of
a 12x1.5mm stainless
steel pipe lasted 1,700
bar and a Tee welded
from a thin-walled
18x0.8mm stainless
steel pipe lasted 480
bar before rupture.
Noteworthy is that the branches’ welding seams did not rupture.
Instead, the material ruptured outside the welding seams of branches
as shown in figure 1.
Larikka CylinWeld (figure 2) consists of a power source, a user
interface for controlling the welding process, a welding chamber and
a fixing cassette for fixing the parts. The fixing cassette is equipment
to which parts can be easily fixed for the welding process. The
positioning devices force parts into a correct position in the cassette
locking them for the welding. The cassette also directs the parts
into proper position in relation to the welding electrode as the
parts are loaded within the cassette into the welding chamber.
Together the cassette and the welding chamber form a shielding
gas atmosphere for controlling the inner and outer shielding gas
during the fully automatic welding process where the movements
of the welding and the power control are executed according to the
pre-programmed parameters. Thus, no special skills or know-how
are required from the person operating Larikka CylinWeld.
Larikka CylinWeld is very suitable for welding diverse and
challenging tubular parts either with saddle weld or straight seams
to collared parts. It is applicable for the welding of single parts
where the part rotates and the welding is down-hand welding, which
theoretically is the most ideal welding situation. Furthermore, with
Larikka CylinWeld it is also possible to weld long manifolds. The
equipment’s functions can be applied so that the pipe is stationary
and the electrode rotates inside the pipe. Since the welding takes
place inside the pipe it is possible to weld branches very close to
each other. Also, the operating range of Larikka CylinWeld is wide:
the smallest diameter is 4mm and the largest 200mm, in special
cases even larger.
Larikka CylinWeld concept and the welding chambers are widely
patented.
Manufacturing tubular parts with Larikka
CylinWeld
Tubular parts have been manufactured under limitations of available
manufacturing techniques and weldable parts have been produced
to meet the requirements and possibilities of the welding. Also, for
Larikka CylinWeld process the parts are prepared by the conditions
set by the welding. The following describes how manufacturing
tubular parts with Larikka CylinWeld works.
Drill and punch
Preparation of parts for the welding is very simple. Firstly, a hole is
drilled to the main pipe. Secondly, an arc is punched to the pipe end
Figure 3
:
Drilled main pipe and punched
branch pipe ready for welding
Figure 2
:
Larikka CylinWeld machine