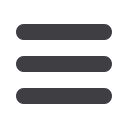

J
anuary
2012
23
›
I
ndustry
N
ews
I
J
G
B
T M P
UT E
...
Exceeds European and other UT Speci cations
Larger Dynamic Range of Gain
Improved Linearity
Selectable Band Pass Filters
Up to 32 Channels
Use with MAC Rotaries or Existing Equipment
HALL 6 F-19
WWW.MAC-NDT.COMFD5
E
®
SPECIALIST pipe measurement technology
company for the oil and gas industry,
Optical Metrology Services (OMS) Ltd, has
completed a pipe measurement and fit-up
project for Subsea 7 on the Exxon Mobil-
operated Oso gas/condensate field off the
coast of Nigeria.
Using its Smart-Fit™ software, OMS
avoided any pipe fit-up problems, providing
Subsea 7 with fast, good pipe fit-ups ready
for the welding stage. Smart-Fit uses pipe
measurement data to predict and control
fit-up, before the pipes are brought into
the bead stall for welding. This prevents
production delays due to poor fit-up and
manages the assembly of problem pipes to
maximise welding productivity.
Onshore in Nigeria, two OMS engineers
used OMS’ PipeChecker™ laser-based
measurement tool to measure the geometry
of the internal walls of more than 1,500 pipe
ends. The pipes were then delivered by barge
to Subsea 7’s pipe laying vessel, Polaris.
Onboard, OMS engineers used Smart-Fit to
sequence the pipes for best fit-up.
Pipe measurement data was made
available to a Smart-Fit station onboard
Polaris. This comprised a laptop located
prior to the firing line. Each pipe in turn was
identified and logged into the software, which
then analysed the fit-up, enabling OMS
engineers to mark the best rotational (and
datum) position on each pipe end.
In the bead stall, these marks were aligned
to achieve the best rotational position so
that pipe misalignment was minimised. Any
problem pipes that would not have fitted
at the specified Hi-Lo were also indicated
in advance so that they could be re-
sequenced or removed. Production delays
due to mismatched pipes were therefore
avoided. Dr Richard Gooch, director of
technology at OMS said: “In order to meet
stringent acceptance criteria for the welds on
this project, Subsea 7 asked OMS to manage
pipe measurement and fit-up, both onshore
and offshore during the pipe laying process.
We are very pleased to report that this project
was extremely successful. Everything worked
perfectly and we managed to avoid any pipe
fit-up problems, which resulted in no delays
to the pipe welding process or repairs.”
This project consolidates OMS’ position as
the leading provider of solutions for pipe fit-
up, including stringent CRA applications. The
Oso oil field is located offshore in the Bight of
Biafra and is Nigeria’s largest offshore gas/
condensate project. Offshore facilities include
eight platforms. A 35-mile seabed pipeline
transports the condensate to storage tanks
located onshore at the Qua Iboe Terminal.
OMS
– UK
Website:
www.omsmeasure.comOMS manages pipe measurement
and fit-up logistics for Subsea 7