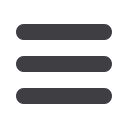

J
anuary
2012
75
›
T
echnology
U
pdate
www.metallurgy-tube-russia.comMetallurgy-Litmash 2012
International Trade Fair
for Metallurgy, Machinery,
Plant Technology & Products
Tube Russia 2012
The International
Tube and Pipe
Trade Fair in Russia
Aluminium/
Non-Ferrous 2012
International Trade Fair
for Aluminium and
Non-Ferrous Metals, Materials,
Technologies and Products
Messe Düsseldorf GmbH
P.O. Box 10 10 06
40001 Düsseldorf
Germany
Phone +49(0)211/4560-7793
Fax +49(0)211/4560-7740
RyfischD@messe-duesseldorf.de www.messe-duesseldorf.de000 Messe Düsseldorf Moscow
123 100 Moscow
Krasnopresnenskaya nab. 14
Phone +7/495/605-1100
+7/499/256-7395
Fax +7/495/605-7207
info@messedi.ru www.messe-duesseldorf.ru2 8 – 3 1 M a y 2012
M o s c o w , R u s s i a
E x P o c E N T R F a i r g r o u n d s
Hydraulic bending
systems for tubes
INTERLAKEN produces hydroforming press systems for use in
tubular part production or materials research applications. The
systems are computer controlled hydraulic press systems with
data acquisition that uses a high-pressure liquid to hydroform
materials. Interlaken’s hydroforming press systems are designed
to embrace both tube and sheet hydroforming applications. Gas
forming systems are also available.
The hydroforming press systems are equipped with Interlaken’s
UniPress control system for reliable and precise control over
the hydroforming process. Easy to use Windows compatible
interface software enables users to build motion and force
profiles designed to fit specific forming needs. The multi-channel
closed loop control system is easily programmed to handle event
as well as time dependencies.
The control system offers dynamic mode switching which
enables the user to switch between a variety of feedbacks such
as force, position, internal pressure and other system variables.
Hydroformed parts are stronger and weigh less due to
structural integrity and fewer welds or add-on pieces. In addition,
costs are reduced and time is saved by eliminating secondary
operations, reducing scrap, lowering material and manufacturing
costs, and increasing design flexibility. With superior control over
forces and motions, Interlaken’s Hydroforming Press provides a
greater overall quality of formed parts.
A dual operation mode provides flexibility. The Learning/
Research Mode determines tool and die specifications, measures
and optimises processes, and programs forces and motions. The
Production Mode runs the optimised profile while monitoring and
recording process variables.
Interlaken Technology Corporation
– USA
Email:
dprill@interlaken.comWebsite:
www.interlaken.comFlux cored product
range widened
HAVING started flux cored wire production in 2009; Gedik welding
has been widening its product range via R&D restructuring that
includes butt and seamless flux cored wire production technologies.
The advantages of flux cored wire are high deposition rate,
smoothness seam, easiest functionality in every position and less
distortion and stress as compared to shielded metal arc welding.
Ever-changing and improving industrial applications create the
demand for flux cored wires.
Gedik
– Turkey
Website:
www.gedikwelding.com