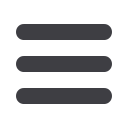

I
nspection,
M
easuring,
T
esting &
M
arking
102
M
arch
/A
pril
2007
Gardner Denver Water Jetting Systems,
USA, manufactures continuous duty
hydrostatic testing units, specifically
for oilfield and pipeyard pipe testing at
pressures up to 20,000psi.
The company produces both diesel and
electric units, which are designed for
portability, and may be trailer or skid
mounted. The units feature an exclusive
‘Pressure-Trol’ system, which allows the
operator to regulate testing pressure and
bleed-down with two centrally mounted
levers, without having to ‘clutch’ the engine
or shutdown the electric motor.
All engine gauges and start/stop controls
are located on centralised control consoles.
Only one operator is necessary to conduct
a complete hydrostatic evaluation, to test
the strength and integrity of drill, production,
and casing pipe.
The electric and diesel units both use the
Partek Triplex Pump, which consists of
components fabricated from precipitation
hardened stainless steel to maximise
corrosion resistance. Pump valve and valve
seats are field replaceable in 30 minutes,
using ordinary hand tools. Advantages
include high testing rates, continuous duty,
elimination of motor and pump interruption,
and 20,000psi working pressure.
Every component of Gardner Denver
hydrostatic testing units is designed with a
specific benefit in mind. The 100 HP T-300
pump includes a power end that transmits
power from the pump driver (either diesel or
electric) to the fluid end. Two standard fluid
ends are offered – the standard
‘L’ for pressures from 8,000 to
15,000psi, and the inline (T-300H)
for pressures from 15,000 to
20,000psi.
All of Partek’s fluid ends are
environmentally safe and share
several
features
including
suction manifolds (from aircraft
grade aluminium), standard ‘L’
style fluid cylinders, and inline
style stuffing boxes and valve
seats (autofrettaged to provide
maximum strength and reliability).
The fluid end is characterized by
minimal internal clearances to
ensure highest possible volumetric
efficiency. Plungers are collet style for
positive alignment and rapid removal.
With thousands in service, the ‘L’ fluid end
for 15,000psi has a simple design that
features easy removal of valves,
plungers
and
packing.
Plungers are colmonoy
coated stainless steel,
a material that is
unaffected by thermal
shock.
With inline operation from
15,000 to 22,000psi, the Partek
Hydrostatic testing units for oilfield and
pipeyard applications
›
A close-up of the patented ‘Pressure-Trol’ valve,
which eliminates the need to stop and restart the
unit for each test, which minimises productivity
fi
(Below) an electric HT-120ES-001 electric hydrostatic tester;
and (bottom) a skid-mounted HT-610ES electric hydrostatic
testing unit featuring V-belt drive, Pressure-Trol, control panel,
and charge pump. The compact design of this unit makes it
practical and popular in pipeyards
Tube
preparation
in perfect
time:
Tube
bending
Tube
end-forming
Complete
solutions
for automation
Maschinenbau GmbH
Hünegräben 22
D-57392 Schmallenberg
Tel +49 (0) 29 72 - 97 15 - 0
sales@transfluid.de www.transfluid.de®