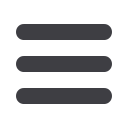

111
M
arch
/A
pril
2007
Otto Junker
– Germany
Fax
: +49 2473 601 600
:
info@otto-junker.deWebsite
:
www.otto-junker-group.comThe principle of a copper tube purging system is
shown in figure 16. The purging station comprises of
an atmosphere supply lance and a clamping lance.
The purging system is connected to one side of the
coils, which means that the oil-laden purge gas is
blown out of the coils and into the furnace chamber.
The inert gas passes through a lance to a manifold
pipe at the tray and then into the tube coil.
This inert gas tube purging system is available for all
the above-mentioned furnace types. The only condition
is indexing product conveyance through the furnace.
Results
Otto Junker have equipped many roller hearth furnace lines with
this copper tube purging system. Examinations have shown that this
reduces the carbon deposits or residual oil inside the copper tube
by up to 90 per cent as compared to furnaces without this purging
system. This satisfies the exacting demands made on copper tubes
for air conditioners.
Inert gas tube purging system
with connection to both coil ends
In this case the inert gas blown through the coils is discharged from
coils and led out of the furnace. The advantage of this system is
data logging of the purging operation is possible. Instruments are
connected to measure flow and pressure of the purging gas flow
to guarantee and record that each coil has been purged with the
required amount of inert gas.
This system requires some special skills of the operators because
the inside of the coil is especially difficult to connect. To date, in
Europe this system has not normally been required.
Oil trap
Evaporation of the drawing oil from the inside and outside tube
surfaces increases the oil concentration of the recirculating inert
gas atmosphere. This oil condenses in lower temperature regions
of the furnace or local to the entry vestibule and cooling zone
where oil drops may form. These drops in turn may reach the
product causing unwanted marks. Hence it is necessary to clean
the furnace atmosphere.
One possibility would be a permanent exchange of inert gas
by permanent input and discharge of a certain inert gas flowrate
but this is of course very costly. Certainly a better solution is the
installation of a filtering system. Otto Junker have designed and
improved such a filtering system in recent years.
The Otto Junker concept for
automatic handling of pancakes
The workflows involved in the heat-treatment of copper tube
pancakes are traditionally labour intensive, requiring multiple
loading and unloading steps.
• Loading into baskets at the coilers
• Loading onto the furnace line
• Removal from furnace line
• Handling in the packing area
These repeated handling operations also increase the risk of
damaging the coils – particularly when thin-walled tubes are
concerned.
With the new concept, only a single loading and unloading operation
takes place between the coilers and despatch. This is achieved
through the use of recirculating coil supports (trays). Moreover,
these steps are robotized, ie all coil handling by human operators
is eliminated.
The return of empty coil trays from the packing line to the coiler is
achieved via a forklift truck or roller conveyors.
A schematic view of this system is given in figure 17.
The benefits of this materials handling concept include the
following:
• Fewer handling operations, meaning a reduced risk of damaging
coils
• Full integration into existing plant configurations is possible
• Capability for full integration of the Otto Junker furnace
• Automation can be introduced in several stages
• Payback period of about 2 years for each loading/unloading
station
4. Conclusion
Based on the complete process route beginning from the metal
melting to the final annealing of the high quality copper tube,
some very innovative technologies for the thermal processes are
available.
Despite the fact that the overview could not touch all areas in detail,
it should inspire technological discussion among the specialists.
›
Figure 17
:
Example of an annealing and packing facility