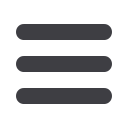

D
rilling,
P
iercing &
P
unching
T
echnology
70
M
arch
/A
pril
2007
The new generation of Hebö tube-drilling
machines are semi-automatic. Only the
fixing of tubes and removal of finished
products is manual. The modular system
can be extended by further working units.
Through combination with a tray-load of
poles and a removal-device the machine
can be extended to a fully automatic plant.
As of September 2007, it will be possible
to combine the RBV12 tube-drilling
machine with Hebö reshaping-machines
(ie embossing-units, bending-machines,
forging-press, passage-heating).
Hebö Maschinenfabrik GmbH
– Germany
Fax
: +49 6453 91 33 55
:
marketing@heboe.comWebsite
:
www.heboe.comStart-Stop process for high
speed precision rollforming
Used for applications such as precise
inline notching and embossing, Dreistern’s
Start-Stop
®
rollforming process was first
developed 30 years ago, and has benefitted
from powerful new drives that have kept
pace with demanding applications. Many
rollforming tasks would not be possible
without the aid of Start-Stop technology.
The rollforming machine works like a
precision press feeder. In the Start-Stop
operation mode, the progressively advancing
profile is stopped briefly during the cut-off
and punching operations The profile is then
reaccelerated to normal operating speed. All
punching and cut-off tools are stationary.
The advantage of this process can be seen
where extensive punching operations are
necessary. The tool designer does not have
to make any compromises due to weight
limitations for the tools. In continuous
operation, all punching and cut-off tools
must be accelerated to the strip speed,
limiting the number and weight of the tools.
In addition, the Start-Stop process offers
advantageous higher production output
rates for short length sections. Rates of 60
sections per minute are normal, while high-
performance lines can reach 120 sections
per minute. The drive system catapults the
profile with an acceleration of up to 8m/s
2
to a speed of up to 100m/min, and stops
exactly at the programmed punching or
cutting position, with a positional accuracy
usually better than ±0.2mm.
Dreistern GmbH & Co KG
– Germany
Fax
: +49 7622 391 205
:
sales@dreistern.comWebsite
:
www.dreistern.comThe Hebö RBV12 is a modular tube-drilling
system for the precise working of tube and
section. The company has been awarded
the Bundesinnovationspreis (Prize of Federal
Innovation) for the RBV12, which is used in
applications such as plant, heating-elements,
rail, staircase and furniture manufacture.
The RBV12 can undertake procedures
including drilling, flow-drilling, thread-forming,
thread-cutting,
core-hole-removal
and
sawing. In addition to a number of special
sections, the machine can be used on round,
square, rectangular and oval-tubes.
Comprising of two drilling units mounted
on a revolving base plate, the RBV12
is adjusted by an infinitely variable feed
carriage. The pivot point of the drilling units
is in the middle axis of the section to be
worked. The base plate can be revolved
under infinite variables up to an angle of
30° to the section middle axis.
Because of the double-sided treatment it is
possible to make precisely aligned through-
bore-holes with an extremely inclined angle.
Each drilling unit can be used for drilling and
thread-cutting. Due to machine construction,
special drilling-tools and a lubrication device,
common problems during drilling of stainless
steel can be avoided. The infinitely variable
adjustment of the tools allows the drilling of
oversizes up to 0.4mm.
Modular, prize-winning tube-drilling machine