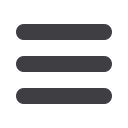

wire
2012
- New Products on show
March 26
th
– 30
th
84
wire
2012
íí
Photo courtesy Rene Tillmann
©
The Eder EDDS-2 system is designed to
revolutionise the rather circumstantial
die-data
storage,
accessibility
and
administration for users of costly wire
drawing die-tools.
Using the EDDS-2 marking unit, a small,
specific and continuously individual
numeric alpha DataMatrix code can be
marked onto the steel casings of each die
in a couple of seconds, and with high
precision. 100% proof of marking quality is
achieved. This DataMatrix code can be
easily read-out and transferred to the
special software, to refer to this specific
die-tool only. All property and performance
data of the die can then be written into the
EDDS software.
Highlights of the integrated EDDS-2 dot
peening solution include high precision
geometrical properties (AS 9132 specifi-
cation) of dots and matrix; precise dot
peening mechanism with an electronically
controlled peening head that grants a
proper reproducible dot and DataMatrix
marking onto steel die-casings; special
Eder EDDS-2 software supports easy and
fast data generation and administration as
well as individual parameter settings for
each application and work piece.
The verification system is specifically
designed to meet the properties (3-
dimensionality) of dot-peened DataMatrix
codes on metal. The system provides
convenient stock analysis features for
parameter set-up of new work pieces and
first-article inspection. Verification results
are kept in the software database, together
with marked data. Images may be saved,
and the operator can trace the properties of
each dot and die.
Eder Engineering GmbH – Austria
Fax
:
+43 1 3674 949 49:
office@eder-eng.comWebsite
:
www.eder-eng.comEurolls SpA
Stand: 11D40
In the field of cold rolling by use of
cassettes Eurolls’ work on research and
development has led to the consolidation
and extension of the application of
microcassettes on special sectors such as
production of welding wire, obtaining very
important results.
Eurolls has reaffirmed its leadership in the
know-how of microcassette application to
various production processes obtaining for
example, and guaranteeing, centesimal
tolerances even on wires with diameter
smaller than 1mm, demonstrating not only
that cassettes technology works but that it
is the Eurolls technology which works.
Also in the machinery field Eurolls has
stood out for innovation and new
technologies.
Proof of this is the recently installed plants
for the production of bead wire for tyres
and the two PC strand production lines
also put into operation a few months ago.
In the first case (bead wire) the
technological innovations introduced by
Eurolls have allowed a sensible reduction in
operational costs withou
t any effect on theline speed, quality and reliability of the wire.
In the second one (PC strand) two lines
were built, delivered and installed a few
months apart, that can reach production
speed of 150m/min, a speed that is
maintained during the whole period of
production with no influence on quality, a
true bench mark in this field.
In the field of construction wire production
the traditional cold rolling line for ribbed
wire has gone through a redesign, and is
now more compact and user friendly.
Again in this field it must be noted the
supply of two production lines for lattice
girder to the Brazilian market, with the
second one entirely built by EdB (Eurolls do
Brazil), the local subsidiary of the group, is
another step in the constant development
and accomplishment of its presence in that
market.
Eurolls SpA – Italy
Fax
:
+39 043 279 6511:
info@eurolls.comWebsite
:
www.eurolls.comGEO-Reinigungstech-
nik GmbH
Stand: 11A34
GEO-Reinigungstechnik will present clean-
ing systems and components for the
improvement of surface quality of long
products like wires, cables, strips and
tubes.
Priority is given in particular to wet chemical
and mechanical cleaning procedures.
Besides GEO’s efficient ultrasonic cleaning
systems, yielding excellent surface quality
even at high processing speeds, the flexible
wiping system ‘Primary Wire Wipe’ will be of
particular interest.
The patented Primary
Wire Wipe (PWW) isdesigned to remove
visible dust andexcessive lubricants from wire and strand
or small strips.
It is an economical, low-maintenance,
environmentally friendly alternative to
traditional wipers such as felt pads or
pieces of rag. In addition, the PWW has
proven successful in applying different
types of lubricants and finishes. The
compact design enables space-saving
installation either in-line or in front of
production equipment for bolts, rivets,
U-shaped staples, etc.
The programme is completed by powerful
air wipes and a wide variety of spiral
brushes with metal and synthetic filaments
in standard sizes and custom-made
versions. The GEO range of equipment
consists of a complete range of ultrasonic,
high pressure, spray and mechanical
cleaning systems for the in-line or off-line
cleaning of wire, strip, cable, tube, rod, bar
and ultrasonic baths for component
cleaning.
GEO-Reinigungstechnik GmbH –
Germany
Fax
:
+49 25 2 9 5552 91:
info@geo-reinigungstechnik.deWebsite
:
www.geo-reinigungstechnik.deGimax
Stand: 10B18
The Robospira/Robobina from Gimax has
had 20 years of success with over 250
machines sold worldwide.
Gimax claims that it was the first company
to produce a fully automated respooler,
and that it has reached a level of
sophistication superior to other currently
available
respooling
solutions.
The
automated respooling machine does not
require an operator for normal operation –
everything is done by the machine itself,
except for changing the bobbin on the
payoff when the wire runs out.
An operator can generally handle up to five
of these machines, changing payoff
bobbins, keeping the magazines topped up
with empty spools, and helping to unload
the finished spools from the storage
conveyor
s. The machine automatically
calculate
s the wire diameter and
compensates for any tolerances in the wire
diameter when precision layer respooling.
❍
Eurolls – reaffirming its leadership
❍
Ultrasonic wire cleaning system –
standard series
îî