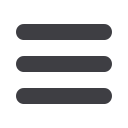

Tube mi l ls and rol l forming
www.read-tpt.com124
S
eptember
2013
Order for automated tube mill
KENT Corporation of Ohio, USA, has
received an order for a new automated
tube mill entry line for an ISO Certified
customer in North America. The
automated entry line will be capable of
24" wide strip and 0.375" thick material.
The entry system will be integrated with
the existing mill for smooth and reliable
operation. The equipment is due to ship
in December 2013.
Kent Corporation has been providing
entry equipment, strip end welders,
accumulators, high-speed cold saws and
tube mill consumables to the tube mill,
roll forming and stamping industry for
more than 40 years. Kent has delivered
over 6,000 pieces of equipment that
are currently running successfully,
with applications that vary from 0.008"
(0.2mm) to 0.750" (19mm) thick and
from strip widths of 0.5" (12.7mm) to
over 80" (2,032mm) wide.
Kent Corporation
– USA
Email:
sales@kenttesgo.comWebsite:
www.kenttesgo.comTube and pipe mills
RAFTER
Equipment
Corporation
manufactures tube mills and pipe mills,
roll forming machines, cutoff machines,
and other related mill machinery. It
is able to provide equipment for tube
sizes from 0.188" (4.76mm) to 16"
(400mm) OD. It has supplied mills using
high-frequency induction (HFI), high-
frequency contact (HFC), TIG/plasma,
and laser welding. Its equipment has
been used for the production of the
following tubular products: mechanical,
structural,
HSS,
energy,
API,
refrigeration, automotive, appliance,
and other tubular products.
Rafter has remained busy throughout
the recent economic downturn. An
RT-3000 automotive tube mill was
commissioned this year for the
production of drive shaft tubing. The
mill is capable of producing tubing up to
127mm OD x 4.8mm wall (5" x 0.188")
with a maximum diameter-to-thickness
(D/t) ratio of 78:1. The line included a
complete strip entry system with vertical
strip accumulator through overseas
partnership. All the drive electrics and
controls for the mill and entry system
were sourced through the US and are
serviced locally. Also included was
a web-based VPN diagnostic portal
that allows Rafter to access the PLC
remotely.
In addition to mill equipment, Rafter
provides mill accessories. These
mainly include weld squeeze boxes,
seam orientation units, and turkshead
straighteners. In the past year, Rafter
has provided many upgrades in these
areas.
For 2013, Rafter will offer a new
machine design for the roll forming
industry. This design will be targeted
for custom roll formed profile producers
that require high-quality machinery with
quick-changeover capabilities. The new
machine will be officially introduced in
November of this year at the Fabtech
International show in Chicago.
Originally started in 1917 as a roll
forming machine builder, the company
was purchased, relocated, and
transformed into a premier tube mill
manufacturer in 1988.
Since this time, Rafter Equipment
has provided nearly 100 tube mills
and more than 400 mill accessory
upgrades. Its focus is to provide
robust equipment that is simple
to operate and maintain. It
supports its equipment through
personalised and dedicated after-
sales service and spare parts.
By doing all of this, Rafter gives
its customers the equipment
necessary to be both successful
and profitable.
Rafter Equipment Corp
– USA
Email:
sales@rafterequipment.comWebsite:
www.rafterequipment.comRafter Equipment Corp – RT-3000
tube forming and welding mill