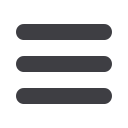

Industry News
www.read-tpt.comS
eptember
2013
19
The World’s No.1 Tube & Pipe Directory
Still No. 1...
...For 13 Years!
Thousands of unique visitors
search our site every day for:
• Manufacturers of tube & pipe machinery
• Manufacturers of tube & pipe products & materials
• Industry news, events and much, much more!
MAKE SURE YOUR COMPANY IS PART OF IT!
Register FREE @
www.tubefirst.comUltrasonic control bench
A FRENCH tube manufacturer has
placed an order to Tecnatom Metalscan
for a new ultrasonic testing bench
using phased array technology for a full
body inspection. Provea will ensure all
the mechanical design whereas M2M
will deliver the full body phased array
electronic equipment.
The complete bench will be delivered
in 2013. The main feature of this
system is its roto-translation capacity:
the tubes have a helical movement in
order to control the entire tube surface
with advanced design for short untested
ends.
The new equipment will allow several
types of defect detection: axial and
skewed cracks, transversal cracks,
delamination and smooth defect. An
ultrasonic thickness measurement
system will also be configured; four
phased array probes will be integrated
into very specific ultrasonic tanks.
The roto-translation motion will
be possible thanks to angled roller
conveying systems. The pitch and the
speed will be controlled directly from
the main HMI. The operator enters
the tube information (diameter, length,
thickness), and the pre-settings are
done automatically. Setting time for
a new tube production campaign
is reduced compared to existing
technology. Two lasers, in charge of
encoding and speed measurement, are
also integrated in the upper frame.
One of the most important technical
developments is the partial immersion
tanks designed for the project. They
will enable the PA probes to come in
contact with the tube without any water
getting inside the tube (no plugging
necessary). The mechanical design
ensures a constant, accurately set
and regular focal distance during the
process.
One of the main advantages of the
future bench will be its flexibility. When
it comes to changing the tube type, very
few settings are necessary. Most of
them will be centralised and controllable
from the control panel. In terms of
speed of control, the bench ensures
the final customer global capacity
target. This value is reached thanks to
several features: an automation system
ensuring a minimal distance between
two tubes (0.5m approx).
Phased array technology and
full parallel M2M method are a key
advantage in terms of productivity.
Provea has an insonification of an area
corresponding to the full length of the
PA probe in 1 shot (gain of productivity).
Therefore, the pitch can be driven up
to 110mm, surface speed 1.5m/sec for
all tubes.
A software supervisor, Lineview,
developed by Tecnatom Metalscan,
manages the whole UT configuration
and operation for calibration as well as
production with the highest flexibility.
Provea
– France
Email:
contact@provea-machine-tube.comWebsite:
www.provea-machine-tube.com