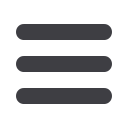

44
Electricity
+
Control
SEPTEMBER 2017
round up
Compact stainless-steel sensor for flexible flow measurement
Selecting the right method and appropriate
device for flow measurement generally in-
volves a time-consuming and resource-in-
tensive consideration of the advantages
and disadvantages of the different systems
and measuring methods. Particularly in the
food and beverage industry, which relies on
high process reliability and perfect hygiene
standards, this means
that there are often a
large number of different
measuring devices for
the respective production
areas. Therefore, the in-
dustry welcomes instru-
ments that reliably monitor the flow of drink-
ing chocolate, beer, olive oil, demineralised
water, or milk, and which are just as precise
in measuring the flow of cleaning agents in
CIP and SIP plants or cooling water in cooling
circuits. They reduce complexity and increase
productivity. This variety of applications is
possible thanks to sophisticated ultrasonic
technology.
Time-of-flight
The DOSIC ultrasonic sensor operates ac-
cording to the concept of time-of-flight differ-
ence: If the ultrasonic signal is sent against
the flow direction, it requires a longer transit
time than the signal sent in the direction of
the flow. The transit-time difference between
the two ultrasonic signals is directly propor-
tional to the mean flow
velocity. The flow vol-
ume per unit of time
is the result of the
mean flow velocity
multiplied by the pipe
cross-section. With re-
gard to reliability and precision in transit-time
difference measurements, the DOSIC sensor
provides an alternative to Coriolis mass flow-
meters, which usually entail high investment
costs. The sensor can detect a wide range
of challenging liquids and media for bever-
age and food production irrespective of their
properties.
Durable and reliable in hygien-
ic conditions
The rugged and compact model
combined with a hygienic design
ensures highly reliable measure-
ment results. The absence of
moving parts in the sensor elim-
inates potential contamination
risks in the demanding hygienic
environments of the food indus-
try. In addition, the sensor has a
straight, seal-free, and self-emp-
tying measuring tube made of
high-quality stainless steel (316L
with Ra
≤
0,8). The high-quality
stainless-steel housing also pro-
vides the necessary ruggedness
and resistance. It therefore goes
without saying that the sensor
has EHEDG certification and
demonstrates FDA conformity.
Since there is no contact be-
tween the sensor and the flow-
ing media, and the flow volume
is determined in a non-contact
SENSORS. SWITCHES + TRANSDUCERS
The IO-Link reduces cabling and
also enables complete control and
monitoring of the sensor in Industry
4.0 machine environments.
The non-contact DOSIC flow
sensor detects the flow volume
of conductive and non-conductive
liquids based on ultrasonic
technology.