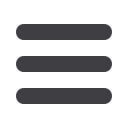

Wire & Cable ASIA – March/April 2008
101
Jay Dorling, general wheelblast sales
manager at the Wheelabrator Group,
believes that those companies who
are unable to invest in new equip-
ment, are putting up with less than
efficient machines and ultimately not
satisfying their customers needs due
to poor blast machine performance.
As many firms will be aware, the
operating efficiency of machinery is
key to achieving maximum output,
optimum quality and maintaining
strong customer relations, but when
efficiency suffers is it time to invest in
something new?
The answer is no, not necessarily.
A common mistake is to immediately
write off or overlook existing mach-
inery. In some cases new is the best
option, but more often than not,
upgrading or modernising an existing
unit reinstates first class production
efficiency, reduces down time and is
available at a fraction of the cost.
Since Wheelabrator introduced its
equipment modernisation programme
(EMP) in 2005, it has helped many
companies capitalise on and extend
the life of existing equipment.
The service is part of the Wheela-
brator Plus division, which also offers
an extensive range of equipment
support services, including training,
maintenance, service, parts, con-
sumables, polyuerethane fixtures and
masking, plus media supplies for
blasting, vibratory equipment and
washing.
The EMP campaign has become
hugely successful and an increasingly
important part of the company’s
business. The unique understanding
of industry needs comes from 100
years’ experience and continual
development in design and manufac-
turing surface preparation equipment.
The newest edition to the programme
is the Titan blast wheel. It is the result
of extensive research and development
and has been designed specifically to
improve the blast performance and
efficiency of existing machinery. It can
be adapted to fit virtually any wheel
blast machine and will lower media
consumption, drastically reduce down-
time and cut production costs and, in
some installations, it has improved
efficiency by more than 30%.
Titan allows for increased space
between blast wheel and the wear
plates, so noise levels are dramati-
cally reduced, creating a better
working environment for employees.
Titan wheels reduce carbon emissons
through energy efficient motors,
making them more environmentally
responsible.
Titan has also recently been awarded
a product innovation accreditation by
the professional jury of trade fair
organiser, Eurofinish.
Just months after they were made
available to the industry, the first two
Titan wheels have been installed in
the UK at painting and blasting
contractors, Broadblast in Sheffield,
as part of their overall company
strategy to reduce waste, decrease
emissions and introduce a recycling
policy.
Wheelabrator – Canada
Fax
: +1 905 319 7561
: wheelabrator@
wheelabratorgroup.com
Website
:
www.wheelabratorgroup.comDon’t suffer because of poor performance