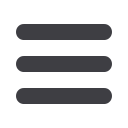

Chemical Technology • May 2015
10
• d is the iron electrode diameter (m),
• D is the copper iron diffusivity (m.s-2пп) ,
• v is the rotation per second (Rps),
• μ is the absolute viscosity (Kg.m/s) and
• ρ is the density of solution (Kg/m
3
).
The exponent of Sc was fixed at 0,33 following previous
theoretical and experimental studies in mass transfer. The
exponent 0,961 was obtained by plotting log Sh versus log Re
(Figure 11), for the conditions: 1166<Re<5840, Sc=1744 35.
The value 0,18 was obtained by a Sh versus SC0.33×Re0.961
(Figure 12). Previous studies on mass transfer at rotating cyl-
inders [23] have shown that for smooth rotating cylinders Sh
increases with 0,7 power of Re. The exponent 0,96 obtained
in this work may be attributed to the surface roughness in-
duced by the deposited copper [23-26] . The above equation
can be used in the design and operation of high-productivity
cementation reactors.
Conclusion
The majority of previous studies on cementation have dealt
with extremely dilute solutions typical of waste water. The
present study is concerned with cementation of copper from
a relatively high concentration of CuSO
4
similar to solutions
Figure 5: ln (C
o
/C
t
) vs. time at different rotational speeds
Figure 6: Effect of pH on the percentage removal of copper ions
Figure 9: ln (C
o
/C
t
) vs. time at different temperatures
Figure 10: ln (K) vs. (1/T)×10
3
at different temperatures
The present study is concerned
with cementation of copper from
a relatively high concentration of
CuSO
4
similar to solutions obtained
by leaching low grade ores and
exhausted copper oxide catalyst
on the rotating iron cylinder. This
design offers high copper ions
removal rates owing to the high
degree of turbulence prevailing at
the surface of the rotating cylinder
even at a low speed of rotation.