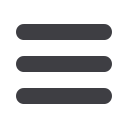

EuroWire – November 2010
50
Compounds & colourings
Melt temperature plays a critical role in the insulation phase of
medium voltage (MV), high voltage (HV) and extra high voltage
(EHV) XLPE insulated power cable extrusion, with organic
peroxides used for cross-linking with both insulation and
semi-conductive materials.
Acceptable extrudate temperature range is limited since proper
melting and homogeneity set the lower limit, while avoiding
premature cross-linking sets the upper limit.
Extrudate temperature can affect both quality of the cable
and the productivity. Premature cross-linking before or on the
screens creates pressure build-up in the extruder and reduces
running time. Premature cross-linking after screens, on the other
hand, may lead to ambers or scorch in the insulation itself.
In continuous vulcanizing (CV) lines the common practise is
either to use thermocouple sensors or to measure extrudate
temperature before start-up using a hand-held meter after
crosshead. Before the introduction of an extrudate temperature
gauge based on ultrasonic velocity there has not been an online
solution available that is both non-contact and reliable.
In the majority of cases extrusion lines are not equipped with an
online melt temperature measurement system to record and to
control plastic melt temperature during the extrusion process.
Normally this temperature is measured only during the
commissioning of the extrusion line at various line speeds and
pressure conditions or later, during servicing.
For this purpose various methods are employed, such as the use
of shielded thermocouples or infrared pyrometers, but each of
these methods has at least minor imperfections.
Using a thermocouple for contact, single-point measurement
has a relatively slow response time. If the thermocouple does not
penetrate into the melt, only the melt surface temperature or the
temperature of the metallic extruder flow channel is measured.
If the thermocouple penetrates into the melt shear heating
errors can occur, presenting a local increase of temperature.
Furthermore the thermocouple influences the melt flow
properties and premature cross-linking takes place.
Using an infrared pyrometer a contact-free temperature
measurement with an improved response time is possible
though, still, mainly the surface temperature of the PE melt is
measured because the penetration depth of infrared radiation
in LDPE (low density polyethylene) amounts to only several
millimetres. Furthermore the presence of specific fillers in the
PE melt can drastically decrease this penetration depth.
The ultrasonic velocity in plastic compounds strongly depends
on the temperature of the material. Therefore it is essential to
compensate this influence if, for example, the dimensions of
plastic insulated power cables (eg insulation wall thickness,
eccentricity) are measured using an ultrasonic technique. On
the other hand, a known temperature dependence of a material’s
ultrasonic velocity can be used to determine the material
temperature by measuring its ultrasonic velocity.
One of the challenges in the measurement of ultrasonic velo-
city in plastic melts is the high ultrasonic attenuation of these
materials.
Ultrasonic temperature
measurement system for
polyethylene melts
by Dr T Clausen of Sikora AG and Dr P Huotari of Maillefer Extrusion Oy
Schematic view of the adapter in the extrusion line
▼
▼
Adapter with measuring
▲
▲
gauge
▲