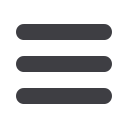

EuroWire – November 2010
51
Compounds & colourings
Ultrasonic PE melt temperature measurement systemUltratemp 6000
The ultrasonic PE melt temperature measuring system consists of an adapter, which
is placed between extruder screw and extruder crosshead. The adapter includes a
high-temperature ultrasonic transmitter and an ultrasonic receiver placed at opposite
sides of the flow channel.
In this way the ultrasonic signal propagates through the entire cross-section of the
PE melt flow (typically 50mm diameter for CV-line insulation extruder) and an averaged
PE melt temperature can be determined in real-time.
An additional pressure gauge is located at the measurement position to record the melt
pressure. This pressure gauge is used to compensate the moderate pressure influence
on the ultrasonic velocity.
Mounted on the outside of the flow channel the ultrasonic sensors do not penetrate
or have any contact with the polyethylene melt and so the extrusion process is not
affected by the sensors. The measuring rate of 100Hz allows a fast response time as well
as the registration of small temperature variations.
During the polyethylene extrusion process an ultrasonic PE melt temperature
measurement system ensures a non-contact, non-invasive, online measurement of
PE melt temperature in real-time, using the temperature and pressure dependence
of the recorded ultrasonic velocity.
Within the capturing of material-specific ultrasonic velocity data this system is suitable
for various polyethylene materials. The measuring accuracy of the melt temperature is
deduced to be less than ±1°C.
For the first time it is possible to accurately measure melt temperature of cross-linkable
PE in CV-lines without disturbing extrusion. With Ultratemp 6000 it is possible to
follow online the most critical variable of CV-line extrusion, thus avoiding premature
cross-linking, maintaining process stability and possibly extending the running time.
It also offers the possibility of feedback control of melt temperature.
Sikora AG – Germany
Fax
: +49 421 48900 90
:
sales@sikora.netWebsite
:
www.sikora.netMaillefer Extrusion Oy – Finland
Fax
: +358 9 886 65 771
:
info@maillefer.netWebsite
:
www.mailleferextrusion.comPlacement of the adapter in the extrusion line
▲
▲