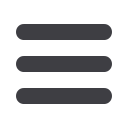
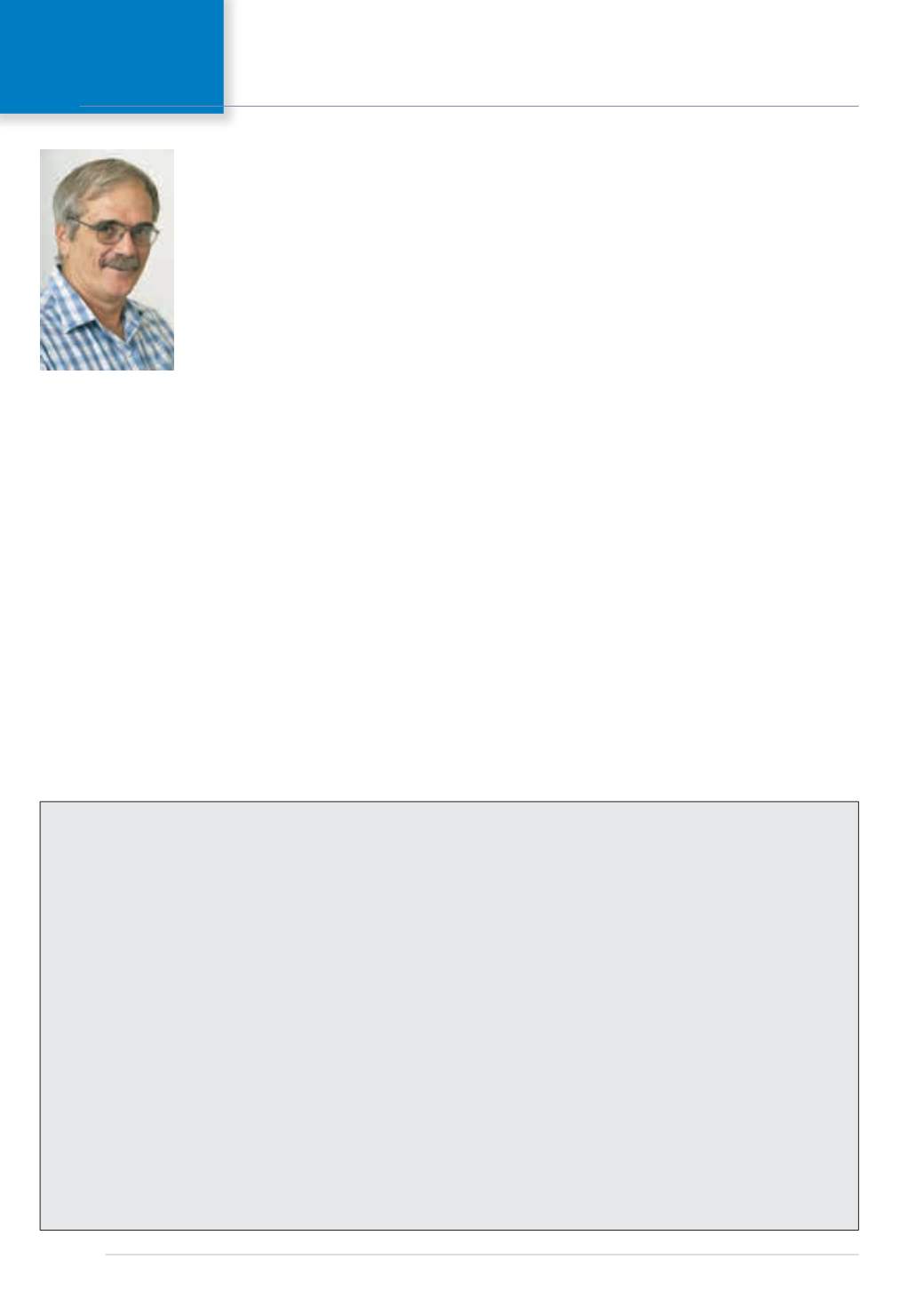
10
MODERN MINING
September 2015
MINING News
Earlier this year profes-
sional services provider
WorleyParsons RSA
was commissioned to
undertake a scoping
study for the position-
ing of a new primary
wet processing plant
for Tronox’s KZN Sands
operation.
KZN Sands is one
of two Tronox mining
ventures in South Africa and concentrates
on removing naturally occurring heavy
minerals such as ilmenite and zircon from
dune sand. The minerals are then either
used as feedstock in their natural form
or in an upgraded form such as synthetic
rutile and titania slag which are produced
through the secondary processing of
ilmenite.
The scoping study, completed by
WorleyParsons over a five-month period,
set out to establish the most economi-
cally viable location for the proposed new
processing plant at the Port Durnford
greenfield site at KZN Sands. To identify the
most optimal position for the new plant,
WorleyParsons RSA developed an innova-
tive methodology, dubbed ‘OptiMap’.
Incorporating various cost relationships
and value chain theory, OptiMap calculates
the optimal costs over the lifespan of a
mine. As the name implies, OptiMap also
provides a visual representation on a map
of the most optimal location of the infra-
structure. The tool has the functionality to
identify cost implications immediately if
the position is changed.
“We are exceptionally pleased with
the development of OptiMap as the use
of this tool gave the WorleyParsons team
an edge. It is an optimisation model
capable of handling the massive num-
ber of possible configurations available,”
says WorleyParsons RSA project manager
Marthinus Odendaal.
Consulting economic- geologist
Vannessa Clark-Mostert adds that locat-
ing infrastructure in terms of the cost
impact it has on the mine is a common
problem that OptiMap now addresses
efficiently. The tool can be used in many
locations and for any mining commodity,
as the same theory and principles apply.
Furthermore, OptiMap is also compat-
ible with other existing WorleyParsons
methodologies such as the EcoNomics™
Delt∆ tool to provide a truly unique value
offering, especially in a discrete options
evaluation environment.
Odendaal and Clark-Mostert go on to
explain that the mineral deposits found in
the sand represent only a small percentage
New technology pins down infrastructure location
of the total sand mined. All the sand and
associated mined minerals are transported
to the processing plant. The heavy metal
is separated and the residual sand then
needs to be returned and rehabilitated
which is why the positioning of the wet
plant was so important.
“For the new Port Durnford site, we had
to establish a position for the primary wet
plant, and the position had a significant
impact in terms of cost,” says Odendaal.
“We first of all had to determine the eco-
nomical mining pit based on the geological
block model using Whittle Optimisation
software. The mine is then scheduled over
the life of the mine and mining blocks
determined. We define all the mining and
process ‘streams’ and express them as a
cost relationship relative to the distance in
rand/tonne/km.
“The distance of the mining block to
the process plant varies over time as min-
ing progress. The total cost over the life
of mine is minimised by determining the
plant position using OptiMap. Here we did
a lot of ground-breaking work for the client
with the use of OptiMap. It was also pos-
sible to advise the client on what mining
method to use as the model made it pos-
sible to determine the total incremental
cost of mining and processing over the life
of the mine.”
Marthinus Odendaal of
WorleyParsons.
Modifications to tungsten plant now installed
AIM-traded Premier African Minerals
Limited, which operates and has a 49 %
interest in the newly commissioned RHA
tungsten project (RHA) in north-east
Zimbabwe, says that previously announced
process plant modifications have been
installed and the operational benefits
confirmed.
The modifications were designed to
improve efficiency of the crushing circuits
and allow better utilisation of the surplus
capacity on the downstream concentration
circuits. The immediate effect of the modi-
fications was anticipated to be an increase
in the percentage of higher grade fines con-
centrate over the coarse concentrate, with
a probable overall increase of total tonnage
of concentrate produced.
Prior to installation of the modifications,
up to 40 per cent of feed ore was rejected
as oversize and stockpiled.
Premier African Minerals says that feed
grade at the mine continues to improve
as the more mineralised ore from within
the resource model envelope is exposed.
When run-of-mine feed grade reaches the
planned grade, RHA expects that produc-
tion targets will be achieved.
RHA is able to produce grade at any
percentage of contained WO
3
(tung-
sten trioxide) from below 50 per cent to
marginally in excess of 70 per cent. The
company’s analysis indicates that at the
current pricing levels of APT (ammonium
paratungstate), the financial returns are
potentially improved by targeting output
at the lower grade as any penalty for any
lower grade concentrate is more than off-
set by the benefits of lower production
costs and a greater tonnage of concentrate
produced.
George Roach, CEO, commented: “I
am pleased to report that the RHA pro-
cess plant modifications notified in our
announcement published on 8 July 2015
have now been installed. This successful
installation was completed simultaneously
with a replacement of the tailings discharge
system. The replacement of this element of
the process plant became necessary due
to design deficiencies only understood
when production increased to the design
throughput of the plant (of not less than
16 tons per hour of resource grade ore, a
mean diluted feed grade target of 0,8 per
cent contained WO
3
and target production
of 5 800 metric ton units per month).
“The modified plant now accepts the
design tonnage into the recovery circuits.
Fine tuning and optimisation is continu-
ing, both as we explore the upper tonnage
limits of the plant in excess of 16 tons per
hour and seek to achieve consistent mate-
rial flow through the recovery circuits. We
expect that as and when concentrate pro-
duction reaches the design output of the
plant, RHA will operate profitably.”