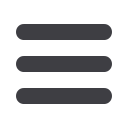

PRODUCT News
52
MODERN MINING
September 2015
Rock that reacts with emulsion explosives
can cause real headaches for blasting per-
sonnel but BME’s double-edged solution
allows customers to quickly identify reac-
tive ground and apply the appropriate
product.
“Among the range of cold emulsions we
have developed over the past 30 years is a
product suitable for use in reactive ground
– an emulsion that is not affected by the
sulphides encountered under such con-
ditions,” said BME GM (South Africa) Albie
Visser.
The problem of reactive ground is
often encountered when drilling in shale
overburden on coal deposits and in the
coal seams themselves. Fine sulphides cre-
ated by drilling can dissolve in the water
in the drill-hole, raising its acidity. This
acidic water can in turn react with nor-
mal emulsion explosive, causing it to heat
up and potentially risk the performance
of the blast – perhaps even resulting in
unplanned detonation.
The first prong of BME’s response was
therefore to develop an emulsion that
would not react under these conditions,
further enhancing the safety of the blast
environment. Emulsion products already
boast a safety advantage, as they are not
explosive until sensitised in the drill-hole;
On-site testing and emulsions solution for reactive ground
BME has developed a double-edged solution that allows
customers to quickly identify reactive ground and apply
the appropriate product.
up to that point, their status as a 5.1 oxi-
diser makes them safe to transport and
handle.
“To establish whether there is reactive
ground on the drill site, our customers
must be able to test the ground conditions,
but sending material for testing can be
time-consuming,” said Visser. “So the sec-
ond prong of our solution is a service that
saves customers valuable time; we have
developed our own in-house ‘tech-truck’,
which includes mobile laboratory facilities
that can be employed on site for testing of
the ground to be blasted.”
The BME team members first conduct a
visual inspection of the site, applying their
extensive experience of blasting in a range
of different conditions. The possibility of
reactive ground can often be indicated
by white patches around the drill holes
– resulting from the high acidity of water
dissolving the sulphide fines.
“If we suspect that the ground may be
reactive, the tech-truck can be brought
in to conduct laboratory testing on site,”
Visser said.
Results from these tests can indicate
where reactive ground may present chal-
lenges, avoiding the risk of discovering the
problem only after the emulsion has been
pumped into the drill holes. This ensures
that blast planning schedules are met and
production is not delayed by unforeseen
blast-related challenges.
BME’s innovative ‘portable laboratory’
has been developed based on research by
universities in South Africa and Australia,
to design and verify a testing procedure
that is effective for dealing with reactive
ground.
BME, tel (+27 11) 709-8765
MCCs ordered for Lesotho diamond project
JB Switchgear Solutions (JBSS) was
recently awarded a multi-million rand
contract for the design, manufacture and
supply of motor control centres (MCCs) for
the Liqhobong diamond mine in Lesotho.
Well-known project house DRA placed the
order on behalf of the client and manu-
facturing is expected to be completed by
March 2016.
The Liqhobong mine is located at the
head of the Liqhobong valley in the Maloti
mountains of northern Lesotho. Ownership
of the mine is held by Firestone Diamonds
(75 %) and the Lesotho Government (25 %).
JBSS’s scope of supply includes eleven
‘Eagle Series’motor control centres, seven of
which will be installed into modified marine
containers and three on outdoor skids.
Incomers are typically rated for 2 500 A at
525V, and fault levels up to 50 kA. Intelligent
electronic overloads are used, and the com-
munication protocol is Ethernet. Starter
sizes vary between 4 kW and 250 kW.
In addition, 16 remote I/O panels,
30 VSDs, 15 soft-starters, 14 DBs, 70 field
isolators and a PLC panel will also be sup-
plied by JBSS.
JB Switchgear, tel (+27 11) 027-5804