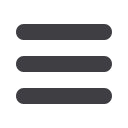

the 2Wper kilogram (0,35 mm thick laminations). Currently, domain re-
fined laser, etc, (at 0,23 mm thick), losses are below 1 W per kilogram.
Amorphous alloy is a very thin material with losses between
0,2 and 0,3 W per kilogram at 1,5 Tesla. Amorphous metals have
come into the electro technical arena, displaying their unique capabil-
ities, but have yet to have all the possible applications and potential
benefits developed.
This material is ideal for transformers where the duty cycle is
low. We have an abundance of distribution and small transformers
throughout South Africa and in these applications we find a low duty
cycle – unlike power transformers. The iron (no-load losses) in a
transformer with a duty cycle of 30% forms 80% of the total losses
of a transformer.
Solid cast iron was useful for some parts of dc machines, but thin-
ner section material was soon in demand for transformers and those
parts of rotating machines that carried rapidly varying magnetisation.
The advantages of the addition of silicon not only reduced eddy
currents, but the effective field permeability of the alloy was enhanced
and other advantages were evident.
Electric steel came into being in response to a need for magnetic
flux enhancers. Excessive power loss owing to lower magnetic grade
steel meant the core steel became hot and magnetic ageing was ac-
celerated. The cost of energy has become such that efficiency is an
important factor from an economical and competitive point of view.
Electric motors
The majority of electric motors are ac motors. Since electric motors ac-
count for 60 to 70%of the electric power energy generated in industry,
it makes sense to explore different methods to improve efficiency in
the consumption of electricity. Improving the efficiency of the motor
helps, but it is comparatively small compared to the energy wasted
by running motors at low – and even on no load – for long periods.
Induction motors are fixed speed machines dependent on the fre-
quency of supply. Until recently, speed control could only be achieved
with slip-ring motors where the resistance of the rotor was changed
using an external resister. This was wasteful of power. Later, power
was recovered using power electronics in a feedback system where
the power from the rotor of was fed back into the system.
Owing to variable duty cycles, many motors run at less than 50%
of their capacity for much of their duty cycle. It is well known that
induction motors are unintelligent and that in these off-load parts of
the duty cycle they consume much more electricity than they actually
need. There are full iron losses and a higher I
2
R loss owing to the fact
that the Power Factor (PF) is poor in a motor running at no-load or
at light loads.
The advance in power electronic and computer technology has
enabled more effective control systems where frequency and voltage
feeding the motor can easily be controlled and optimised, enabling
power savings.
Induction motors can be controlled so that the speed optimises the
load requirements by adjusting the speed accordingly; further savings
can be achieved by reducing the voltage according to the load require-
ments. To take into consideration the possibilities of high frequency in-
duction motors, motor steels will become thin and pure with low alloy.
Therefore the rising frequency regime can be faced without too
1
12
ENERGY EFFICIENCY MADE SIMPLE 2015