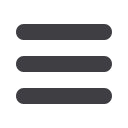

would be 88 – 64 = 24 degrees.
The loss due to misalignment is
proportional to the cosine of the
deviation from normal. Cos24 =
0,9135 which represents a loss
of 8,6455%.
A simple way around this
would be to make a manual
adjustment of the panel’s ele-
vation occasionally.
The system could be syn-
chronised daily by returning the
array to the vertical position
(corresponding to 6:00) after
sundown, ready for the next
day). Rotation would com-
mence at 6:00 facing East.
Test rig construction
Figure 2
is a photograph of the
test unit. On the right hand is
the fixed panel and the rotating
panel is on the left. Note the
black levelling screws and the
red bull’s eye spirit level used to level the rig. All parts were machined
on the company’s computer controlled router.
The outer frame of the steering mechanism is at a 26 degree an-
gle to the (level) base and is rotated by a synchronous one revolution
per day motor.
The inner frame has provision for adjustment to compensate for
the seasonal variations in the sun’s path. The brass pipes provide a
means to align the panels at right angles to the sun at 12:08, corre-
sponding to our position of 28 degrees East, and pointing due North.
In both cases the shadow of the pipe was the size of the pipe base.
At this point the motor was started.
The motor had been purchased as providing clockwise (CW) ro-
tation and we had naively assumed that this referred to the rotation
direction looking at the output shaft
side. With the publication deadline
looming, we discovered that the ro-
tation was counterclockwise (CCW).
‘Houston, we have an anomaly!’
We replaced the motor and fortu-
nately all was well.
The panels were rated at 1,5 V
500 mA, so they were terminated
with 2,2 Ohm resistors, giving about
one Volt at midday. Both panels
provided outputs within 2% of each
other.
Figure 3
shows the connections
to a Techlyn datalogger board. The
board provides:
• Eight 12 bit analogue inputs
(0 - 5 V)
• Two 12 bit analogue outputs (0 - 10 V out)
• RS232 communications port
• 4 line character Liquid Crystal Display (LCD) port
• Embedded microchip 18F252 processor
System operation
The analogue signals were read at one second intervals for one min-
ute, then averaged. The same arithmetic was performed for an hour.
Finally, the hour totals were added to give a day total. Logging started
at 07:00 and continued until sundown.
Graphing was performed by the economically priced and easy to
use MakerPlot program. All the system power was derived from a
battery backed sinewave inverter.
Figure 3: Connections to a datalogger board.
Figure 4: Plot screen. Note the built in averaging function below the meters.
1
25
ENERGY EFFICIENCY MADE SIMPLE 2015