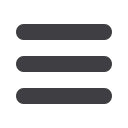

Technology
news
Wire & Cable ASIA – September/October 2010
46
In wire manufacturing, salt carriers are frequently part of the coating system that
is applied before drawing. On high carbon wire salt carriers are used as a basis
for the drawing process, on top of conversion coatings or on a bare surface. Their
function is the separation of die and wire, and transfer of lubricant into the
forming die.
The sophisticated composition of the products gives a reduced sensitivity against
humidity and so low water pick up on the coated wire. This provides a good
corrosion protection even during long storage periods.
Traditionally borax, or formulations containing borax, are used for this application.
Recent investigation of the toxicology of borax and boric acid initiated by the
European Union has shown that borax acts as a reproduction-toxic substance.
Borax has since been classified as a toxic substance with a Reprotox category 2
(or according to the GHS System: Repr. 1B). This reclassification presents a new
situation for the wire drawing industry. New handling techniques are required for
these toxic substances and stricter environmental regulations have to be applied
in the production plants.
Reducing borax content in salt carriers below the limit of declaration could,
perhaps, be an interim solution. However, such a measure is questionable, not
only because future legal regulations can hardly be predicted.
The challenge for Chemetall was to formulate salt carrier coating products
completely free of boron. The result of Chemtall’s R&D efforts is a range of new
boron-free carrier coatings for different applications. First formulations have been
tested successfully in industrial applications in Europe.
Among the newly developed and tested products is Gardolube
®
SC 6226. Its
properties are at least comparable to carriers containing borax that are still in use
in the market.
Chemetall GmbH – Germany
Website
:
www.chemetall.comBoron-free salt carrier coatings
Ultratemp 6000 is Sikora’s latest
development for the power cable
sector. It is a non-contact polyethylene
melt
temperature
measurement
system, based on non-invasive
ultrasonic technology. It is specifically
tailored to the production of medium
voltage (MV) and high voltage (HV)
XLPE insulated power cables.
The system precisely measures the
melt temperature during production
without influencing the melt flow
properties, as the ultrasonic sensors
are positioned outside of the flow
channel. Melt shear heating effects do
not occur.
Besides temperature measurement,
the
Ultratemp
6000
detects
discontinuities in the melt. Early
cross-linking after screens which may
lead to ambers and scorches in the
polyethylene material is avoided. The
extremely high measuring rate allows
a fast response time as well as the
registration of small temperature
variations.
Ultratemp 6000 is described as an
important step for further process
optimisation and costs reduction
during the production of MV and HV
cables.
Sikora AG – Germany
Fax
: +49 421 48900 90
:
sales@sikora.netWebsite
:
www.sikora.netMonitoring melt temperature
Ultratemp 6000 measures the melt
m
m
temperature and detects discontinuities