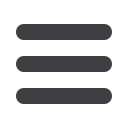

News
Technology
March 2017
49
www.read-eurowire.comEUROBEND is setting new standards in
mesh production by offering the “AMM”
and “AKK” series of innovative flexible
mesh welding lines covering every mesh
application.
Both the AMM and AKK are well
established and can be found operating
in leading precast and mesh producing
companies in Europe, Russia, the Middle
East and North America. Different models
are available for both the economic and
high output production of mesh, offering
maximum flexibility without changeover
adjustments, due to unique design and
functionality of the wire feeding and
welding module.
They are designed for the production of
standard and customised mesh designs
and sizes, allowing the welding of uneven
line and cross wire lengths and different line
and cross wire diameters within the same
panel, and mesh used in various precast
wall panels with openings (for doors and
windows) due to the servo-driven moving
welding head.
Depending on the machine version, line
and cross wires are fed fully automatically
from two Flexi-line Rotor straightening and
cutting machines with automatic diameter
changing system (patented) or from pre-cut
wires/bars.
Equipped with single or double Y-axis
programmable,
servo-motor
driven
welding head configuration with four
or eight welding points (PL X-Y AMM
series) or multi-head configuration with
up to 81 fixed welding heads (PLC AMM
series), the new AKK welding line has
set new standards in mesh production.
This innovative design eliminates all idle
times and at least doubles productivity
in comparison to conventional welding
lines. All advantages from off-coil and
pre-cut welding machines and more are
combined in one machine.
The AKK Series is capable of producing
large and small orders consecutively
without any downtime. The concept
behind the AKK series allows automatic
mesh spacing and dimensions changes,
making it the only flexible high
production coil-fed mesh welding line,
as it can produce all mesh types instantly
without any adjustments. It also offers
a compact system layout requiring
minimum floor space requirements.
Benefits include no downtime when
changing, and wire coils, wire diameters,
wire and mesh dimensions.
Equipped with the patented “Automatic
Wire
Orientation
System”,
which
allows the use of a high speed roller
straightening module for line wire
feeding, the “AWOS” absorbs all wire
straightening imperfections from the
roller straightener. This unique Automatic
Wire
Orientation
System
ensures
perfectly flat mesh panels regardless of
wire and straightening quality. It is fully
programmable and capable of processing
all types of material, smooth or ribbed.
A single coil replaces all line wire
de-coiling stations, where a double line
and cross wire de-coiling station ensures
continuous operation. As a result, minimal
stock of wire spools and coils is required
and the necessity for large stock of ready
mesh as in conventional welding lines is
eliminated.
Multiple diameter changes during one
day/shift can be achieved efficiently due to
single coil line wire feeding.
Eurobend GmbH – Germany
Website
:
www.eurobend.comSetting new standards