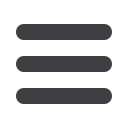

News
Technology
March 2017
54
www.read-eurowire.comPLASMAIT from Austria is seeing an
increasing demand for its high-output
plasma heat treatment lines for stainless
steel products. The next deployment
of its PlasmaAnnealer will take place in
Southeast Asia.
Plasmait sold a 30kW plasma annealer to
a renowned stainless steel wire producer,
who wants to replace its traditional tube
furnace for production of flat ferritic and
austenitic product with widths up to 30mm.
The HPA30 plasma annealer with output
capacity of 100kg per hour will allow the
manufacturer to halve the energy cost per
kilogram of output whilst allowing for a
considerable cost saving in terms of peak
power consumption.
Much
lower
power
connection
requirements of the plasma annealer also
means cheaper cabling installation for
connecting power.
The new compact single-line production
will have the same output as the old
multi-line furnace and will take about one
third of the shop floor space. A single-line
production will also reduce material
manipulation and limit the investment
into the associated takeups, payoffs and
transport system.
A typical plasma annealer installation
for stainless steel applications can
substitute around ten traditional lines on
a conventional strand furnace.
Plasma
annealer
allows
accurate
heat input and hence more uniform
recrystallisation, which is reflected
in homogeneous grain size in the
longitudinal and transversal direction.
The HPA30 annealer also features an
extended tempering zone to allow for
extended dwell time or slow cooling,
which is necessary for selected ferritic
grades of stainless steel.
The
new
annealer
combines
the
advantages of high speed bright
annealing and scratch-free surface finish.
Processed material does not touch
the plasma chamber when at high
temperature, which reduces the risk of
surface scratching.
This is different to the conventional strand
furnace where tubes remain in contact
with the furnace guiding supports
also during the maximum elevated
temperatures when they are most
vulnerable to surface damage.
A unique feature of plasma annealing is
that heating is conducted in low-pressure
inert atmosphere, for which a vacuum
installation and accurate material guiding
are necessary.
The advantage of a vacuum system is that
purging gas (usually hydrogen or forming
gas) is supplied at low pressure, which
reduces overall purging gas consumption.
Plasmait GmbH – Austria
Website
:
www.plasmait.comMore demand for high-output plasma heat
treatment lines
▲
▲
Annealer for flat stainless steel wires and profiles
In an engine, seven types of screws out of
approximately 70 are considered critical,
and are crucial to achieving the engine’s
specified design performance: bolts for the
cylinder head, crankshaft, con rod, flywheel,
and main bearing cap, as well as for the
camshaft cap, camshaft sprocket andVCT.
Having developed specialised engine
expertise over three generations, the
Italian
fastener
company
Brugola
OEB Industriale SpA has focused on
manufacturing these critical bolts.
When Brugola recently opened its first
factory in the USA, the company sought
to expand into the American market as
well as enhance the precision of its critical
engine bolts.
Before
the
company
opened
its
Plymouth, Michigan, plant, one of its
key investments in guaranteeing the
quality of its engine bolts was to select an
advanced, sophisticated gauging system.
In order to make certain that all of its
fasteners were flawless, Brugola turned
to a high-speed 360º laser gauging
device. The machine uses eight sensors
and real-time part velocity calculation to
essentially create a 3D profile of each part,
along with measurement of a wide range
of user-defined features to determine
if each part meets exact dimensional
requirements.
The device Brugola selected for its critical
fasteners, called the GI-360, measures a
number of crucial fastener features such
as head and shaft diameter, lengths,
straightness, concentricity, thread angle
and diameter (including major, minor
and pitch diameter). It also detects any
damaged threads, along with cracks on
the bolt head and flange.
Brugola turned to a leading gauging
equipment
manufacturer,
General
Inspection, to develop a number of novel
inspection features.
When the fastener inspection system
manufacturer worked to improve the
accuracy of dimensional measurements,
the result was a redesigned version of the
device, the GI-360T, which includes a tilt
and lift feature for the laser head.
With Brugola’s dedication to zero-defect
manufacturing of its critical engine
fasteners, the company sought to further
enhance the fastener inspection system.
As an option on its high-speed fastener
inspection system, Brugola selected an
axial viewer lens system for 360º head
crack detection.
In support of Brugola’s goals, General
Inspection improved crack detection
in order to detect cracks, scratches or
missing features on the side flange of
bolts. This speciality lens ‘sees’ around the
head of the part.
Brugola OEB Industriale SpA – Italy
Website
:
www.brugola.comPushing the limits of fastener manufacturing